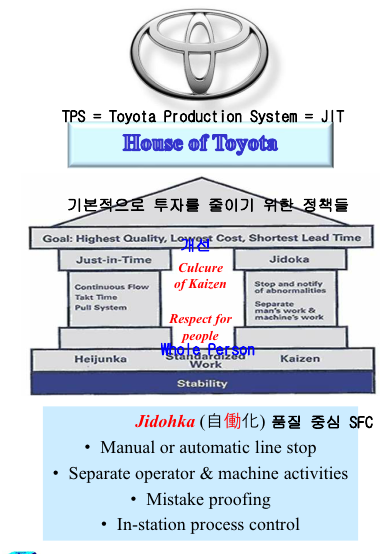
- Jidohka (자동화) = 품질 중심 SFC
- Manual or automatic line stop
- Separate operator & machine activities
- Mistake proofing
- In-station process control
- Repetitive Mfg
- 소품종 대량 ↔ 다품종 소량
- Ass'y + Fabrication
- Line : MRP w/o W/O = 워크 오더 없이
- Fab : flow batch vs. JIT
- push vs. pull
1. Introduction
1) Toyota and Japanese Manufacturing
Before Toyota, Japnese products were cheap and of poor quality
Vision of SONY in the 50's
"Become the company most known for changing the worldwide image of Japanese products as being poor quality"
"일본 제품의 품질이 나쁘다는 세계적인 이미지를 바꾸는 것으로 가장 잘 알려진 회사가 되라"
-1950
- labor strikes after the brink of bankruptcy in 1979 → Life long employment.
1979년 파산 직전의 노동 파업 → 종신 고용
- Revised with a US military order of 5000 vehicles for korean war
- 50's ~ 60's
- treid to copy the Ford's Rouge complex near Detroit
- Failed by the limited resources available at that time, and then developed the TPS
- Japanese manufacturing during the vietnam War
- US cargo ships returned witht cheap japanese products
- E. Deming's contributions to Japanese manufacturing
- When organizations focus primarily on quality, quality tends to increase and costs fall over time
- When organizations focus primarily on costs, costs tend to rise and quality declines over time
- 70~90's
- steep grouwth after the 1973 oil crisis, and became one of leading carmakers
- launch of lexus in 1989, prius in 1997
- 2010
- suspended sales of 8 vehicle models, and paid 1B to settle a lawsuit
2) Overview of TPS and Its Clones
Japanese manufacturing came into the spotlight after the oil shocks in the late 70's
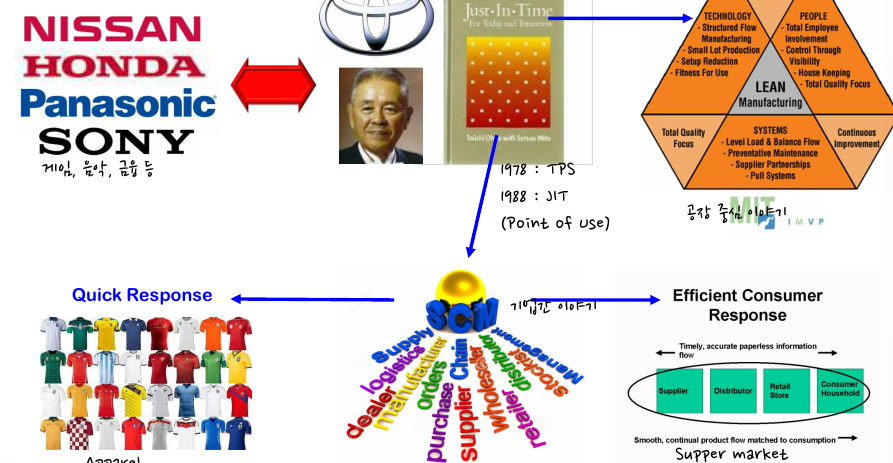
3) JIT principles
JIT is a key building block for moderm approaches to MPC, and is both a philosophy and a set of techniques
- Stabilizing and leveling the production schedules are prerequisites to effective JIT
생산 일정의 안정과 평준화는 효과적인 JIT를 위한 전제 조건이다.
→ MPS with time Fensing
- Acchieving very short lead times supports better customer service and responsiveness
짧은 리드타임을 이륙하는 것은 고객 만족과 반응성을 이끌어낸다
- Reducing hidden factory can be at least as important as reducing costs
숨겨진 공정을 줄이는 것은 가격을 하락시키는 것만큼 중요하다
- Implementing the whole person concept reduces distinctions between white and blue collar workers
종신 고용을 진행하는 것은 사무직과 생산직의 구분을 줄인다.
- Cost accounting and performance measurements need to reflect the shift in emphasis away from direct labor as the primary source of value added.
원가 계산 및 성과 측정은 부가가치의 주요 원천으로서 직접 노동에서 벗어나 강조되는 변화를 반영해야 한다.
- JIT must be modified for nonrepetitive applications
JIT 는 비 연속 공정을 위해 수정되어야 한다
- JIT is not incompatible with MRP-based system
JIT는 MRP 기반 시스템과 호환되지 않는다
1. JIT in MPC
1) Major Elements of JIT or TPS
JIT Primarily focuses on back-end execution but extends beyond MPC
JIT 는 주로 백엔드 운영에만 초점을 맞췄으나 MPC까지 범위를 확대하고 있다.
(1) An approach to minimize waste "muda" - in manufacturing
생산에서 낭비(muda)를 최소화 하기 위한 접근법
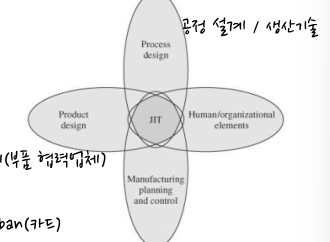
- Process, movement, methods 프로세스, 운동, 방법론
- Product defects, waiting time 상품 결손, 대기 시간
- Overproduction, excess inventory 과대 생산, 과대 재고
- Unused people skilss 사용하지 않은 인적 능력
(2) A broad philosophy of pursuing
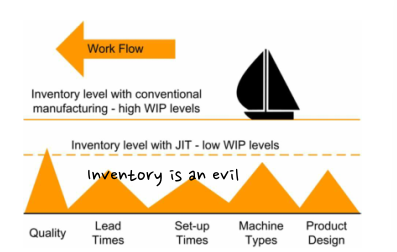
- zero inventories 재고 없음
- zero transactions 전표 없음
- zero disturbances 불량(혼란) 없음
(3) Important features of JIT
- Elimination of batches, reduction of WIP 배치의 제거, WIP의 감소
- Leveling production schedule, direct ties to vendors
생산 스케줄의 평준화, 하청업체(부품 협력 업체)와의 직접적인 연결
- Visual controls without paperwork and complex overhead
서류와 복잡한 간접비 없이 시각적인 통제
← kanban for work order ; work order 를 제외한 kanban(카드)
(4) action programs of JIT
a) Reduction of setup times and lot sizes
setup 시간과 lot size의 감소 - SMED, Heizunka
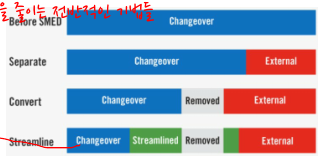
- SMED (Single Minute Exchange of Die) : Setup time 을 줄이는 전반적인 기법
- Separate internal and external setup 내부와 외부 setup을 구분
- Convert internal to external 내부를 외부로 바꾼다
- Streamline internal setup 내부 설정 간소화
- Eliminate(waste in) adjustments
b) A no defects goal in manufacturing
생산에서 결손 없음의 목표 - Poka-Yoke, Jidohka
- TPM (Total Productive Maintenance)
- Schedule PM before breakdown 고장 전 PM을 스케줄
- Give operators a sense of responsibility for their machines
운영자에게 기계에 대한 책임감을 부여합니다. (작업자가 기본적 유지보수)
- Train and empower operators to perform routine maintenance on their equipment.
작업자로 하여금 그들의 장비의 일상적 유지 보수를 행할 수 있도록 권한과 교육을 부여한다
- 5S : Sort(정리), Shine(청소), Simplyfy or set in order (정돈), Standardize 정리 정돈, 청소 유지, Sustain (훈육; 마음가짐과 습관화)
- Reduce downtime, increase process flow
작동하지 않는 시간을 줄이고 프로세스 플로우를 늘인다
- Visualization
c) Kaizen
- A focus on continual improvement 지속적인 개선에 초점
- =forced improvement, continuous improvement
d) TOC, 5 Whys
- Worker imvolvement 작업자 참여
- 분임조, 근본 원인을 따져 보아라 ; not to do 를 정해야 한다
e) cross-trained worker
- 한 사람이서 여러개의 일을 할 수 있다
- Cellular manufactruing
f) Quality in TPS
(5) Benefits of JIT
- Throughput time reductions, reduced changemover time (SMED)
처리 시간 단축, 변경 시간 감소(SMED)
- Less material movement, space reduction
더 적은 자재 이동과 공간 축소
- Reduced transactions, simplified MPC, quality improvemnt
줄어든 전표, 간단해진 MPC, 품질 개선
- Inventory reductions, labor cost reductions, quality cost reduction
재고 감소, 노동비 감소, 품질 비용 감소
- Greater responsiveness to market demands 시장 수요에 대한 뛰어난 반응성
- More satisfied / cohesive workers, better team working
보다 만족스러운/응집력 있는 직원, 더 나은 팀 작업
2) JIT Impact on MPC
(1) Impact on Back-end
- Greatly streamlined execution on the shop floor and in purchasing
현장 및 구매 시 실행이 크게 간소화됨
→ Routine execution ; SCM 관계
- Eliminate standard shop-floor reporting systems → Hidden Factory
표준화된 shop-floor 보고 시스템을 삭제한다 → 숨겨진 공정
- Detailed shop scheduling (W/O, P/O), WIP, → Kanban
상세화된 shop 스케줄링 (W/O,P/O), 공정중재고 → 칸반
- Pay the vendor for the purchased components in each period
공급업체에게 각각의 기간동안 구매한 부품들을 정산
→ Backflushing 후정산 ; VMI
(2) Impact for front-end
- More stable, level (Heizunka), daily-mix schedules → Fixed MPS
- 최소 1달 고정 ; 3달을 예고
(3) Impact on engine
- Reduce the number of part number planned and the number of levels in the BOM
계획된 부품 번호 수 및 BOM의 레벨 수 감소
- Planning is at the level of assemblies without detailed planning
세부 계획 없이 조립품 수준의 계획 수립
→ Phantom Bill
- not for MRP Explosion ; W/O 만들지 않음
3) The Hidden Factory
Factory processing transactions on papers and computer systems → major source of overhead
종이와 컴퓨터 시스템의 공정 처리 전표 → 간접비의 주요 원인
(1) Types of transactions
- Logistical transactions
- ordering, execution, and confirmation of materials
자재의 주문, 실행, 그리고 확증
- Receiving, shipping, expediting, data entry, data processing, accounting, error follow-up
입고, 배송, 신속화, 데이터 입력, 데이터 처리, 회계, 오류 후속 조치
- Balancing transactions
- verify that an activity actually occurred 활동이 실제로 일어났는가를 입증
- Production control, purchasing, master scheduling, forecasting, and customer order processing
생산 제어, 구매, 마스터 스케줄링, 예측, 그리고 고객 주문 프로세싱
- 10 ~ 20 % of the total manufacturing overhead costs
전체 생산 간접비의 10~20 % 차지
- MRP planning can be cut by 75~90 % in complexity
MRP 계획은 75~90 %의 복잡도를 줄인다.
- Quality transactions
- Extended far beyound quality control 품질 관리 이상의 확장
- Identification and communication of specifications, certification, recording of back-up data
사양 확인 및 전달, 인증, 백업 데이터 기록
- Change transactions
- changes of engineering/ master data (routings, BOM, specification)
공정과 마스터 데이터 (경로, BOM, 사양)의 변화
- Engineering change transactions are some of the most expensive costs
공정의 변화는 가장 비용이 많이 드는 것이다
← ECN= Engineering Changing Notice
(2) How to reduce the cost of hidden factory
- Reduction / elimination of the number of transactions ; Stabilized operations
전표의 수를 줄이거나 제거한다 ; 공정의 안정화
- Automation of transaction 전표의 자동화
4) JIT Building Bocks in MPC
→4 Fundamental building blocks
(1) Production design
- Standard parts, modular design, DFM (=Design for manufacture) in cells
셀 내 표준 부품, 모듈식 설계, DFM(=제조용 설계)
← CE; Concurrent engineering 동시 공학
- Appropriate and achievable quality, reducing the # of BOM levels
적절하고 실현 가능한 품질, BOM 수준의 수를 줄이기
(2) Process design
- SMED (setup reduction), Quality improvement(Jidoka; 서양의 Automation = labor을 줄이는 것), Cellular manufacturing(U-shaped cells)
- Bandwidth of the process 프로세스의 대역폭
; Capacity to take on some variation → Flexibility or Agility
변화를 줄 수 있는 능력 → 유연성 혹은 민첩성 ( 대역푝 ; 유연성 << 민첩성 Agile)
(3) Human / organizational elements
- Continual improvement 지속적 개선, corss training and education
- Whole person cencpet
- more than muscles → Employee involvement and empowerment
- Empower employees to make decision → Jidoka or Line-stop
- Andon = 안전등
(4) MPC
- Kanban = eliminate detailed material planning 상세 자재 계획을 삭제하는 것
- work-order 을 대체 ; work order with pull 후공정
- BOM with 2 ~ 3 levels
- Hidden factory reductions, MRP interface
5) Modular Design
- Reduce the # of platform(chassis)
: costs, times 속의 내용물은 같고 외부만 다르다
- platform : a basic architecture of a vehicle family
- Case : Volkswagon's lego blocks
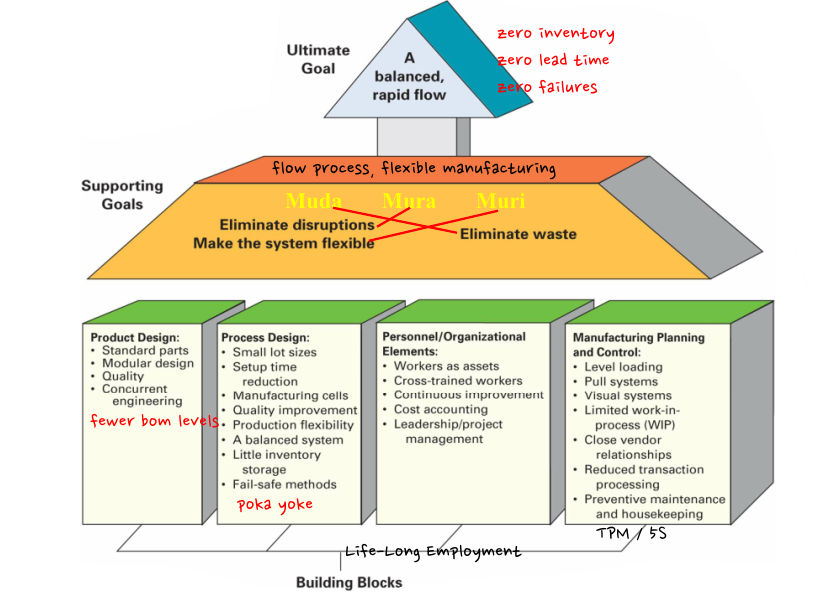
2. JIT Example : Muth Pots and Pans Co.
1) Product
2) Leveling the Production
Heijunka schedule
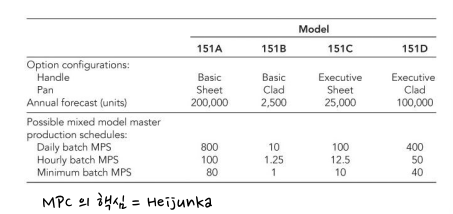
- Converting the forecasts to the daily requirements for each model
예측을 각 모델의 일별 요구량으로 바꾼다
- 250 days / year, 8 hours / day
3) Pull system introduction
(1) Pull system of continuous flow production
연속 flow 생산의 pull system
- production matches customer damand rate or takt time
생산을 고객 수요 혹은 유휴 시간에 맞춘다 = Demand rate와 일치시킨다
- Processing without waiting, 1-piece flow, no inventory, demand pulls through the system
대기 없는 공정, 낱개 생산, 재고 없음, 시스템을 통한 수요 당기기
(2) Pull system ↔ Push system
- Produce only when there is a need for more parts in a downstream(user) work center
하류 작업장(후공정)에서 더 많은 부품이 필요할 때만 생산한다
- Prerequisites 전제 조건
- lot size reductions 랏 사이즈 감소
- limited WIP 공정 중 재고의 제한
- fast throughput 빠른 처리량
- Guaranteed quality 인증된 품질
- Signals for needs 필요의 시그널
- golf ball, yelling, container / tote, cards(kanban), designated space
(3) Muth's case
-
Empty containers are used as the signal for more production
비어있는 컨테이너는 더 많은 생산을 위한 시그널로 사용된다
-
Two major issues 두 개의 주요 문제
- Stability of production plan 생산 계획의 안정성 → at least 1-month frozen
- Container size : size commonality, congestion, proximity, setup cost,...
-
Examples : Part # 137 (basic handle)
(4) Movement under pull system
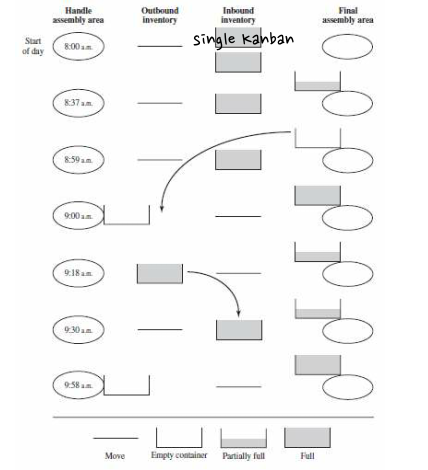
- 2 full container signal handle assembly to stop working
2 개의 전체 컨테이너 시그널이 assembly 로 하여금 업무를 중단하도록 한다
- Final assembly consumes stock until container is empty
컨테이너가 비워질 때까지 최종 어셈블리가 재고를 소비함
- Empty Container returned, signaling handle assembly to begin working
비워진 컨테이너가 반환되면 시그널이 다시 assembly 를 작업하도록 하낟.
- Final assembly uses second container while first is refilled
마지막 어셈블리는 첫번째 것이 다시 채워질 동안에 두 번째 컨테이너를 사용한다
- Full container is returned to final assembly for usse
다 채워진 컨테이너가 마지막 공정에서 사용되기 위해 반환된다.
4) Product Design
- Example : Handle redesign → Modular Design
- Components before re-design 재설계 이전의 부품
: handle ass'y = hand set + handle base + ring + rivets
- Redesign for common parts 공통 부품의 재설계
: common parts except the handle grip
- Advantages from the redesign 재설계로 인해 얻어지는 이득
- Reduction in inventory for different handle bases
서로 다른 손잡이 베이슬로 인한 재고의 감소
- Simplified BOM
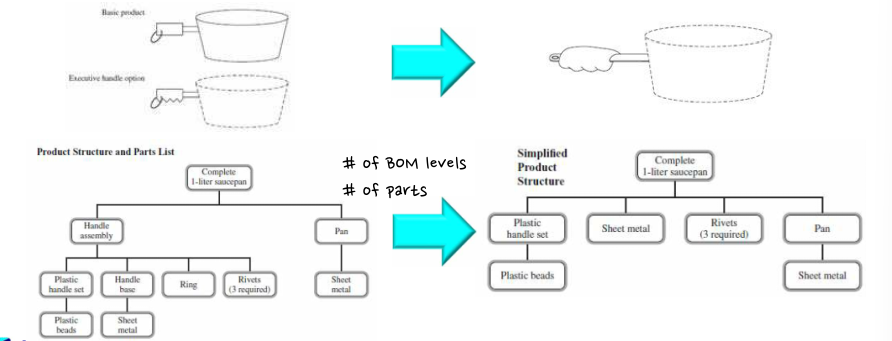
- Concurrent Engineering ↔ DFM, DFA, DFL
; Manufacture, Assembly, Logistics
5) Process Redisgn
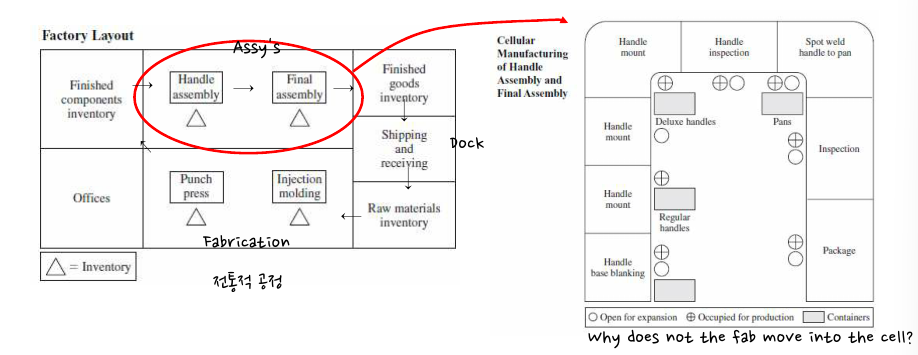
- Redesign 재설계
The same equipment used for attaching both kinds of plastic handles
이러한 종류의 플라스틱 핸들을 접착시키는데엔 동일한 설비를 사용한다
- Product redesign allows rethinking factory layout
제품 재설계를 통해 공장 배치를 재고할 수 있다
→ Cellular manufacturing for handles
- Visible inventory management, less inventory, and shorter product flow distances
가시화된 재고 관리, 재고의 감소, 그리고 생산 플로우 거리의 감소
- Quality improvement is required 품질 개선이 필요하다
6) BOM Implications
Effects on redesign and cellular manufacturing 재설계와 cellular 생산의 효과
- Components : reduced from 14 to 10 부품의 종류와 개수가 ↓
- The handle base and handle ass'y no longer exist in inventory
손잡이 베이스와 손잡이 부품들은 더 이상 재고에 존재하지 않는다
- Phantom bill : used for part # 137, the handly ass'y
- Cellular manufacturing
- Shorter lead times : 5weeks → 2weeks
- Reduced WIP inventory, bettere response to the market
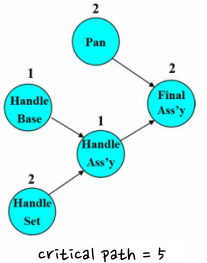
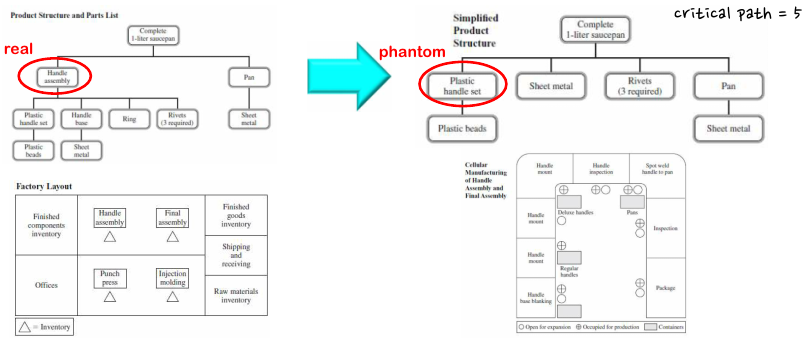
3. JIT Applications JIT 적용
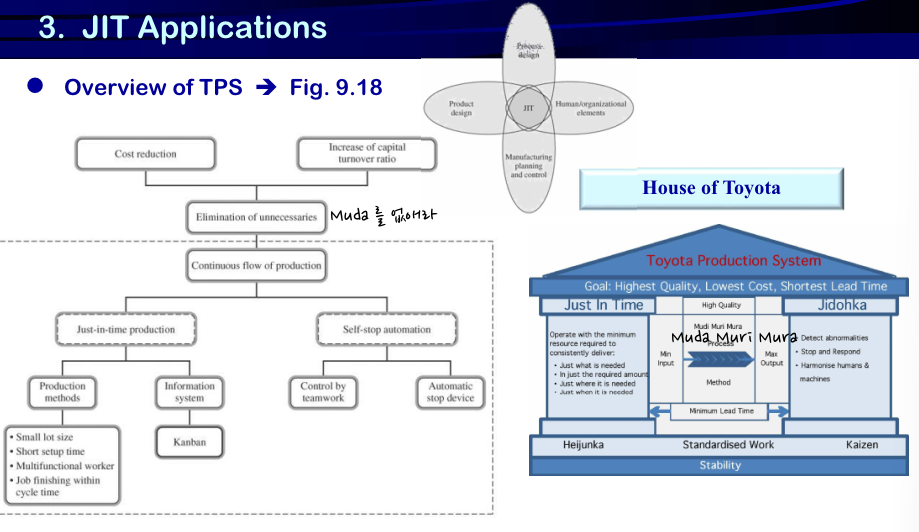
1) Single-Card Kanban ↔ Two-card kanban
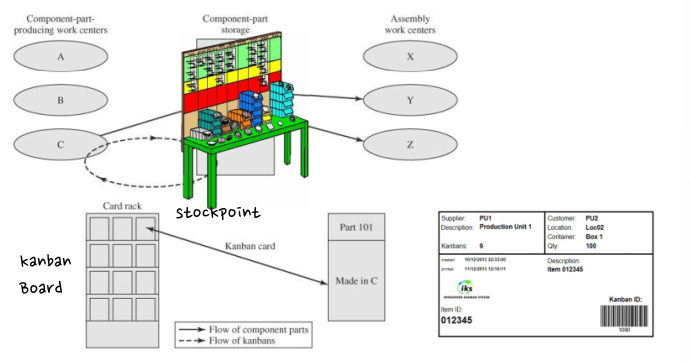
- Kanban authorizes the production of a part by each workstation
Kanban은 각 워크스테이션에서 부품의 생산을 승인한다.
- The number of kanbans = the max WIP inventory
칸반의 수 = WIP 재고의 최대
- The greater the number of kanbans, the alrger the inventory, but also the autonomy of workstations
kanbans의 수가 많을수록 인벤토리는 커지지만 워크스테이션의 자율성도 커진다
2) Toyota's Kanban System
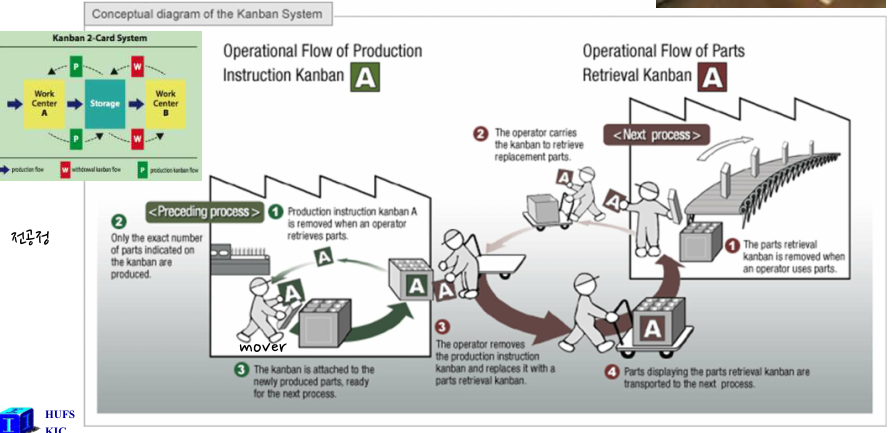
- Two-card kanban
- kanban system for intermediate storage 중간 저장을 위한 칸반 시스템
- Retrieval (or conveyance, move), production kanbans
검색(또는 운송, 이동), 생산 칸반
- How to determine the number of kanbasn
- The number of kanbans =
Y=aDemand×LeadTime×(1+α)
- α : policy variable (safety stock) → should be less than 10 %
- a: container size → should ≤ 10 % of a day's requirement
- Toyota's guidlines for the kanban system
- Each container of parts must have a kanban card
각각의 부품의 컨테이너는 칸반 카드를 가지고 있어야 한다.
- The parts are always pulled 부품들은 항상 이끌린다
- No parts may be obtained without a conveyance kanban card
운송 칸반 카드가 없으면 부품을 구할 수 없다
- Standard containers only can be used for a part
표준화된 컨테이너는 오로지 부품을 위해서만 사용되어야 한다
- No extra production (without a production kanban) is permitted
생산 칸반 없는 추가적인 생산은 허가되지 않는다.
3) Limits of JIT
JIT is developed for high-volume repetitive manufacturing
JIT는 많은 연속 생산의 가정 하에 발전되었다.
- Limited number of end items and parts 제한된 수의 최종 품목 및 부품
→ Minimize Mura Mura의 최소화
- Frozen MPS at least for a month → Constant flow
- level capacity for equipment and labor
- Extra capacity is required → Life long employment
- Use capacity productively : QC circle, TQM
- Limited application of digital techs
- The TPS may sacrificed the system responsiveness and flexibility for the stability fo production
TPS에서는 생산의 안정성을 위해서 시스템 반응성과 유연성을 희생시켰다.
4. Nonrepetitive JIT
High-volume flows lines and level loading are not efficient for low-level production
대용량 흐름 라인과 레벨 로딩은 저레벨 생산에 효율적이지 않습니다.
1) A service Enhanced View of Manufacturing 향상된 제조 서비스 관점
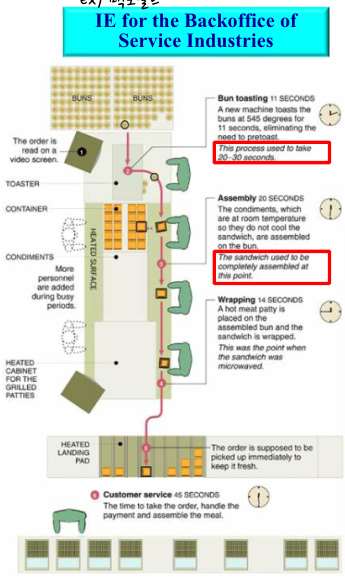
(1) Characteristic of Service Operation 서비스 운영의 특징
- High variability 높은 다양성 : demand and services
- Limited use of automation 자동화 사용의 한정성
- Cannot maintain inventory 재고를 유지할 수 없다.
(2) Requirements of Modern Manufacturing 현대 생산의 요구
- Increasing the number of product / service combination → Servitization
늘어나는 제품과 서비스의 결합 → 서비스화
- End-item forecastting is more difficult 최종 제품의 예측은 더 어려워졌다
- Larger buffer inventories are unacceptable
더 큰 버퍼 재고는 허용되지 않습니다.
- Operation 1) 운영 2) 작업순서(공정) ; 소품종 대량생산 → 다품종 소량 생산
2) Flexible Systems
- The basics of JIT can be successfully implemented for nonrepetitive manufacturing
반복되지 않는 제조를 위해 JIT의 기본을 성공적으로 구현할 수 있다.
- Product engineering, process engineering, whole-person concept,...
- Example : a telecommunications Equipment Manufacturer
- JIT applied to its high-volume repetitive products
대량 반복 제품에 적용된 JIT → ABC 분류
- Inventory turns tripled, WIP reduced by 75%
재고가 3배 증가, WIP 75% 감소
- Failure rate in manufacturing reduced by 50%, setup times reduced in 50%
생산에서 고장률이 50% 감소했으며 setup 시간이 50% 감소하였다.
- JIT then applied to its low-volume nonrepetitive products
- Cellular manufacturing is introduced, while MRP si still used for overall planning
Cellular 생산이 도입되었음에도 MRP는 아직까지 전체적인 계획에 사용되고 있다
- First-pass yield increased by 27% in the first 6 months
- Manufacturing cells under JIT hit 100 % of schedule
수율 > 직통율 (W/O rework)
3) Simplified Systems and Routine Execution
- Work must flow through the factory so quickly that detailed tracking is not required
작업이 공장을 통해 신속하게 진행되어야 하므로 자세한 추적 작업이 필요하지 않다.
- Weekly Wash
- Sales orders of week 1 become the production schedule of week 2
week 1의 sals order 은 week 2의 생산 스케줄이 된다
- Emphasis changes from scheduling material to scheduling time blocks
자재의 스케줄링에서 타임 블록의 스케줄링으로 중요도가 바뀌었다
(생산 좌석제)
- Schedule like a set of train
- assign order only to a time frame 시간대에만 주문을 할당하다.
4) Push (MRP) vs. Pull (JIT)
Type |
Characteristics |
Push(Line;소품종 대량;MTO/JobShop) |
Pull(Line;다품종 소량; MTS/ATO) |
Market Requirement |
Product design |
Custom |
Standard |
Product variety |
Broad |
Narrow |
Individual product vol / period |
Low |
High |
Ease of changing total volume |
Easy / incremental |
Difficult |
Ease of changing product mix |
Less difficult |
More difficult |
Delivery speed |
By schedule |
By FGI |
Manufacturing related |
Process Choice |
Low-vol batch |
High-vol batch & line |
Organizational control |
Centeralized |
Decenteralized |
WIP |
High |
Low |
5. Lean Production by APICS
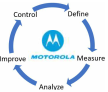
Lean Production ← Lean Manufacturing ← TPS
1) Lean Six Sigma (M. George, 2002)
(1) 3 principles for shortening lead times
리드타임을 줄이기 위한 3가지 원칙
-
Predict lead time by capping amount of WIP
WIP 상한선을 기준으로 리드 타임 예측
→ CONWIP = CONstant WIP
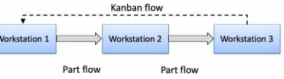
-
Maintain SC velocity by maintaining an even flow of WIP
WIP의 흐름을 균일하게 유지하여 SC 속도 유지
-
Prevent excess WIP by releasing material into the line in amounts consistent with batch sizes
배치 크기와 일치하는 양으로 자재를 라인에 방출하여 WIP 초과 방지
(2) Implementing the principles
원칙의 실행
- Pull system
- takt time to control the velocity of flow and reduce ovall L/T
유휴시간으로 흐름의 속도를 조절하며 전체적인 리드타임을 줄인다
- Strategic buffer
- serve demand during manufacturing L/T ← Unique to Lean
생산 리드타임 동안 수요를 충족 ← Lean 에만 있다
- Process flexibility 프로세스 유연성
- flexible machinery, corss trained employees, quick changeovers
2) Lean Thinking (Womack and JOnes, 1996)
- 5 principles of lean : value, value stream, flow, pull, perfection
- Major improvement tools : VSM, Pull system, setup reduction (SMED), TPM
(1) VSM = Value Stream Mapping
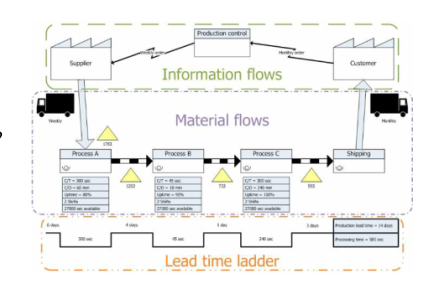
- A visualization tool showing steps from raw materials to customer
원자재에서부터 고객까지의 단계를 보여주는 시각화 도구
- Major task
- Add a form or feature to the product? 상품에 형태 혹은 특징을 더할까?
- Enable a competitive advantage? 경쟁 이점을 달성할 수 있는가?
- Price, delivery, fewer defects
- Add value that the customer is willing to pay?
고객이 기꺼이 지불하고자 하는 가치를 더할 수 있는가?
(2) Heijunka
(3) 5s
- 정리 (Sort), 청소 (Shine)
- 정돈 Simplyfy or set in order
- 청결 Standardize : 정리, 정돈, 청소를 유지
- 훈육 Sustain : 마음가짐과 습관화
(4) Hoshin Kanri 방침 관리
- 7-step process for strategic planning
- MBO = Mgmt By Objective
4) Integration of Lean and MRP/ERP
(1) Pull vs. Push System
Lean = pull System | a pull created from customer demand and downstream workstation on the shop floor 고객 수요와 shop floor의 하류 작업장에서 만들어지는 pull |
---|
MRP = Push system | materials are pushed to and through work centers as a result of W/Os and P/Os 자재는 W/O 와 P/O 의 결과로 작업장에 밀려진다. → Planning is never perfect 계획은 완벽하지 않다 |
(2) Leveraging the strength of lean and MRP / ERP
- Advantages of lean
- Reduce LT, improve quality, and minimize the inventory
- Weakness of lean
- Not efficient when productsa are complex ← BOM-based MRP
생산품이 복잡하면 효과적이지 않다
- Not Efficient when demand is bumpy or highly variable
수요가 불안정하거나 변동이 심한 경우 효율적이지 않음
← Lean, only if CV <=0.3 ; CV = Coefficient of Variance = μσ
- Lean 6 Sigma :
Lean falls apart when you use a part only every 3 months
3개월에 한 번씩만 부품을 사용하면 린(Lean)이 무너진다
(3) Repurposing ERP
- Order point logic that responds to downstream demand signal → electric Kanban
하류 수요 시그널에 대해 반응하는 주문 시점 로직 → 전기 Kanban
- Kanban quantities determined by lot-size calculator : scrap, setup, runtime/unit
칸반의 양은 랏 사이즈 계산에 의해 결정된다
- Shop floor data collection by MES/ERP MES/ERP에 의해서 모야진 Shop-floor-data
- Portals for suppliers to upload planning parameter data
공급업체가 계획 매개변수 데이터를 업로드할 수 있는 포털
: LT, scrap, production status (SRM→eSRM)
6. Joint-Firm JIT
JIT must be applied with suppliers JIT는 공급자와 함께 사용되어야 한다
Toyota has 540 consolidated subsidiary and 226 affilates
도요타는 540개의 연결 자회사와 226개의 계열사를 보유하고 있다
1) The Basics
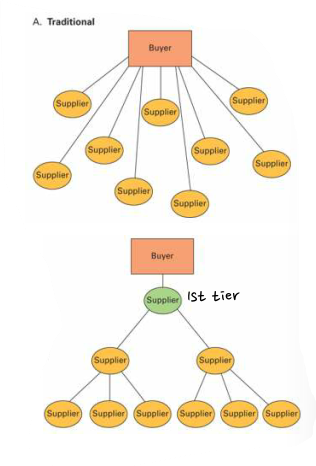
(1) The most important prerequisites 가장 중요한 전제
- Stable schedule 일정한 주문
- Otherwise, inventory will move from the warehouse to trailer trucks
그렇지 않으면 재고가 창고에서 트레일러 트럭으로 이동한다.
- Coordinated execution 협업적인 실행
- material supply without intervention of indirect laber personnel
간접 노동자의 개입이 없는 자재 공급
- Reduced vendor base 공급 업체 기반 감소
- The number of vendors reduced by as much as 90%
공급 업체의 수가 90% 가까이 줄어들었다.
(2) Common practices 일반적 관행
- Blanket orders 포괄 주문
- shipping orders given in a very short period before the shipping date
선적기일 전에 아주 짧은 기간에 이루어진 선적지시서(납입지시)
- No inventory record and inspection 재고 내역과 조사 없음
- Direct delivery to the line ← 무검사, VMI
- Eliminate record keeping by backflushing 후정산에 의해 지켜진 기록 삭제
2) Tightly Coupled JIT Supply 긴밀하게 결합된 JIT 공급
Example
a seat supplier and a auto manufacturer 좌석 공급 업체와 자동차 제조업체
→ Excellence in execution is essential
- Exact build sequence before 30hours : models, colors
30시간 전에 정확한 빌드 순서
- Direct delivery to the assembly line → no seat inventory in the line
어셈블리 라인으로의 직접 배송 → 라인 상에 seat 재고가 없다
- Paid by backflushing completion of cars off the line
완성된 자동차가 라인을 빠져나갈 때 후정산 처리 된다.
3) Less Tightly Coupled JIT Supply
Alternative solution 대체안
pick-up at the vendor's warehouse on some pre-arranged schedule
일부 사전 예약 일정에 따라 공급업체 창고에서 픽업
- Savings in transportation costs 운송비용의 절감
→ Consolidated transportation 통합 운송
- Stability and predictability 안정성과 예측성
- eliminate the uncertainty inherent in vendor deliveries
공급업체 제공에 내재된 불확실성 제거
- Reduce hidden factory costs 숨겨진 공정 비용을 줄인다
- Packaging costs, return to vendor costs
4) JIT Coordination through Hubs
VMI based on the Hubs
- Inventory visible to both customer and supplier 공급업체, 고객 모두에게 보여지는 재고
- The supplier has knowledge of exact customer usage
공급업체는 고객 사용을 알고 있다
→ no forecast and surprise orders 예측 혹은 급한 주문이 없다
- The supplier is in the uphill skier mode
- The supplier is responsible for supply, but can choose whatever ways it wishes
공급자는 공급에 대한 책임이 있지만 원하는 방법을 선택할 수 있다.
5) Lessons
Not shift the execution problems from the customer back to its suppliers
실행 문제를 고객에서 공급업체로 옮기지 않는다
- Joint problem identification and solution 공동 문제 식별 및 해결
- A focus on joint (chain) measures 공통 (chain) 측정의 집중
- The need for stabilized schedules 안정화된 스케줄의 필요성
- Help from the customers for the suppliers to implement JIT with their suppliers
공급업체가 공급업체와 함께 JIT를 구현할 수 있도록 고객의 지원
7. JIT Software
Most ERP systems include software that support JIT execution
대부분의 ERP 시스템은 JIT 실행을 지원하는 소프트웨어를 포함한다.
1) The MRP-JIT Separation
- Split into JIT items and non-JIT or classic MRP items
JIT 와 비JIP(고전 MRP)로 나뉜다
- Procedure for JIT items JIT 절차
- JIT MPS → JIT Planning with phantom bills → JIT execution with e-based system
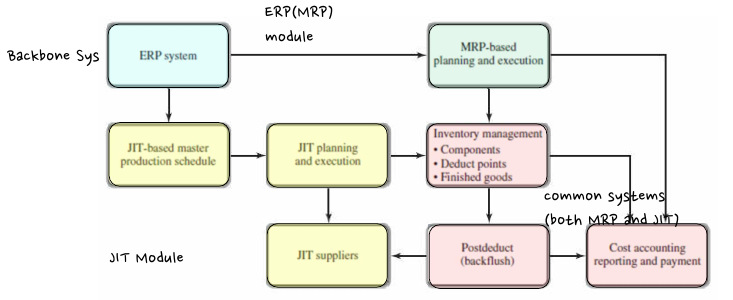
2) JIT Planning and Execution
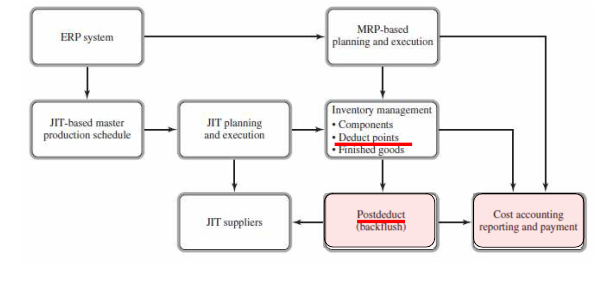
- JIT Planning and execution is driven by a daily build schedule
JIT 계획과 실행은 일간 빌드 스케줄에 의해 유도된다
- Deduct point
- A stage in the manufacturing process where the inventories for certain parts are back-flushed
특정 부품에 대한 재고가 후정산되는 제조 공정 단계
- Need to migrate from MRP-based planning to JIT-based planning/execution
MRP 기반의 계획에서 JIT 기반의 계획/실행으로 옮겨야할 필요성이 있다.
8. Managerial Implications
JIT is best seen as an integrated approach to achieving continued manufacturing excellence
JIT는 지속적인 제조 우수성을 달성하기 위한 통합 접근 방식으로 가장 잘 알려져 있다.
- Information System Implications
- MPC systems should support continuous improvement in reengineered manufacutring processes
MPC 시스템은 재설계된 제조 공정의 지속적인 개선을 지원해야 한다.
- Manufacturing Planning and Control
- JIT has profound implications for all detailed MPC activities
JIT는 모든 상세한 MPC 활동에 깊은 영향을 미친다.
- Scorekeeping ; life-long employment ↔ life-long employability
- JIT requires fundamental changes in reward systems and managerial scorekepping
JIT는 보상 시스템과 관리적 평가 지표를 근본적으로 바꾸는 것을 필요로 한다
- Utilization of capital assets 자본 / 자산의 활용
- Not as important as responsiveness and material velocity
반응성과 자재 속도만큼 중요하지는 않다
- Direct labor cost 직접 노동비
- Distinction between direct and indirect is not useful
직접과 간접의 구분은 중요하지 않다.
- Pros and Cons
- Simple product structures and level schedule 단순한 제품 구조와 일정한 스케줄
↔ nonrepetitive schedules under MTO MTO 하에 있는 비연속 스케줄
- JIT operations are at great risk without the discipline of MRP
MRP의 규율 없이는 JIT 운영이 매우 위험하다
9. CPIM Questions
JIT systems replace discrete manufacturing batches with
a. Work in process
b. Kanbans
c. Production rate goals
d. Cellular manufacturing
answer : c
In JIT system, the goal is to reduce which of the following Factors?
I. Setup times
II. Defects
II. Forecast Errors
a. I only
b. II onlyy
c. I and II
d. I and III
answer : c
The whole person concept refers to
I. Limiting the use of part-time workers
II. Direct labor employees performing nontraditional tasks
III. Having all workers physically producing products
a. I only
b. II only
c. III only
d. I and II only
answer : b (floater = 다기능 담당자)
In a two-container Kanban system, workers at the supplying work center always keep two full containers in reserve to accomodate surge demand
a. True
b. False
answer : b
Considering the following information, what would be the correct number of kanban cards for this system?

a. 1
b. 2
c. 3
d. 4
answer : 100 * 4 / 250 x (1+0.8) = 2.88
Advantages of hub inventories include which of the following
I. Lower costs due to reduced damage to goods
II. Increased visibility for both supplier and customer
III. The supplier has knowledge of demand and usage pattern
a. I and II only
b. I and III only
c. II and III only
d. I, II, and III
answer : c