1. Introduction
1) Vicious Cycle of Bad Capacity Execution
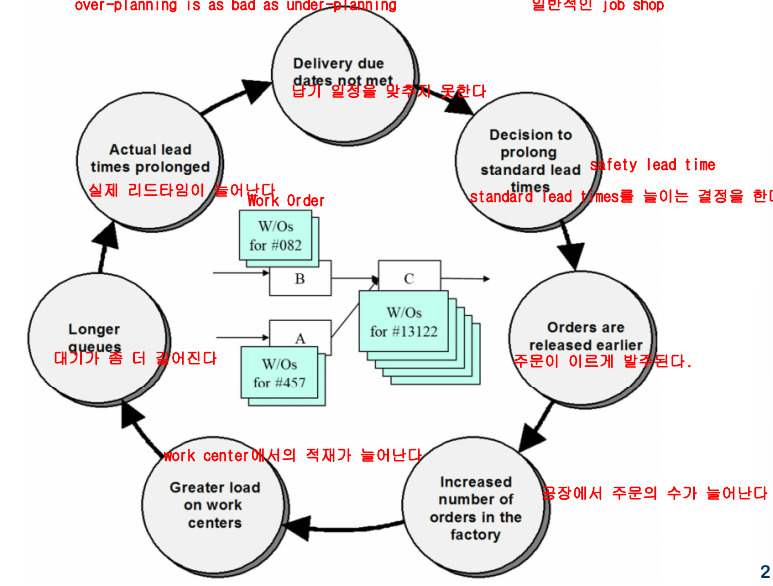
2) Definitions of Capacity
(1) Demonstrated (or Measured) Capacity
- Figured from historical data 역사적 데이터를 통해 나타내어 진다
→ Math average
- Example
- Working hrs of 4 period = 110, 140, 120, 130
→ Demonstrated capa = (110+140+120+130) / 4 = 125 hrs/ period
- 6 periods output in unit = 580, 565, 575, 570, 590, 560
→ Avg. output = 573 units & Std. hours / unit = 0.2 hr/ unit
→ Demonstrated capacity = 573 x 0.2 = 114.6 hrs / period
(2) Rated (or Calculated Capacity)
RC(Rated capacity; 정격용량) = Total Time X A X U X E
: adjusted by available time 가용 시간, utilization 가동율, and Efficiency 효율
- Available time 가용시간
- Depends on the number of machines, workers,and the hours of operation
기계의 숫자, 인적자원, 그리고 작업 시간에 따라 결정된다.
- Availability = (Number of hours a work center can be used) / Total working hours
= work center 가 이용할 수 있는 전체 시간 / 전체 작업 시간
- Utilization 가동율
- The % of time that the work center is active compared to the available time
실제 가용할 수 있는 시간에 대해 work center 가 움직일 수 있는 시가
- Utilization = Actual hours worked / Hours available
= 실제 일한 시간 / work center 에서 가용한 시간
- Efficiency 효율
- the % of standard hours of work produced compared to the actual hours worked
실제 근무 시간에 비해 생산된 표준 근무 시간의 백분율
- Efficiency = Standard hours produced / Actual Hours worked
= 표준 근무 시간 / 실제 근무 시간
Example
A WC consists of 6 machines that are available 16 hrs per day for 5 days a week. Utilization is 80% and efficiency is 110%. what is the rated weekly capacity?
RWC = 6 16 5 80 % 110 % = 422. 4 hrs / week
2) Framework of Capacity Management
(1) Capacity Management 용량 계획
- Establishing, measuring, monitoring, and adjusting limits of capacity to execute all mfg schedules
모든 생산 일정을 실행하기 위한 용량 제한 설정, 측정, 모니터링 및 조정
- Tradeoff among objectives 목표간 균형 조정
- Low working capital & fixed cost 낮은 노동 자본과 고정비
↔ High service level, short L/T & high delivery reliability
높은 서비스 레벨, 짧은 리드타임, 높은 운송 신용도
(2) Phases of Capaccity Management : Planning → Controlling
- Subject to the manufacturing environment : continous flow ↔ repetitive mfg ↔ service, process
a) planning phase : RC, RCCP, CRP
- Issues
- how much / many, where, when of resources
얼마나 많이, 어디서, 언제 자원을 사용할 것인가
- EG: labor, shifs / overtime, part-time workers, equipment, materials, subcontractors (외주, 하청)
- Determine resources needed for the priority plan (MPS / MRP)
우선순위 계획에 필요한 자원의 결정
- Translate the plan into capa requirement 계획을 자재 수요로 바꾼다.
→ BOM including routing info 라우팅 정보를 포함한 BOM
- Sum up capa requirements for each time period and each resource
각각의 시간 시기와 각각의 자원에 따른 용량 수요 전체 합
→ Load profile 작업 부하 (Work load)
- Validate the requirements 수요의 확정
- Resolve differences between available capa and requirements for each time pereiod
가용한 용량과 각각의 시기에 따른 수요의 차이를 해결한다.
b) Controlling phase : PAC ↔ SFC
- Monitor output and comparing it to plan and make adjustments as necessary
산출을 모니터링하고 그것을 계획과 비교하여 필요에 따라 조정한다.
3) Introduction
How to check the capacity requirements implied by a production plan(MPS) or planned orders(MRP)
생산 계획(MPS) 혹은 계획 주문(MRP)에 포함된 용량 요구사항을 확인하는 방법
Why not open order → executable 해야한다.
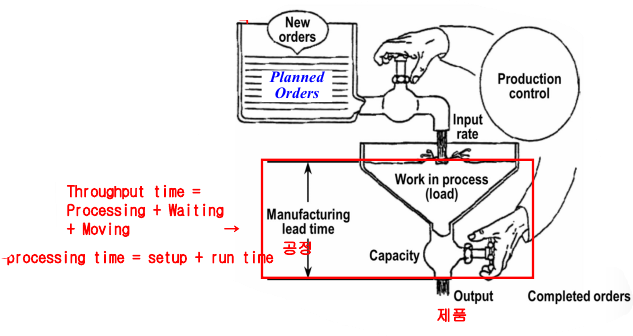
(1) Major Issues in Capacity Planning 용량 계획의 주요한 쟁점들
- How to match the capacity with the plans : increase or ffix capacity
계획과 용량을 어떻게 일치시킬 것인가 : 용량을 늘리거나 고정시키는 방법
- Trade-off between faster throughput time (LT↓) and reduced capacity utilization
빠른 처리 시간과 낮아진 용량 사용의 상충관계
(2) Capacity
- The ability to produce output per period
용량 = 단위 시간당 산출물을 생산할 수 있는 능력
- Level : workstation 작업자 << work center 작업반 << line/plant
(3) Load(or workload) 작업 부하
- the amount of work scheduled released for a specific span of time
단위 시간 동안 계획된(혹은 발주된) 작업의 양
- Throughput time = Processing + waitting + Moving
- processing time = setup + run time
(4) MRP : Infinite Loding
- Does not explicitly consider capacity constraints
용량 계획을 외재적으로 고려하지 않는다.
2. The role of Capacity Planning 용량 계획의 역할
The feasibility of plans depends on materials and capacity
자재와 용량에 따라 계획의 가용성이 바뀐다.
1) Hierarchy of capacity planning Decision 용량 계획 결정의 계층
- RP → RCCP → CRP → Finite Loading (possilby by APS) → I/O Analysis
- APS = Advanced Planning and Scheduling, Adv. Production Schduling, Adv. Planning System
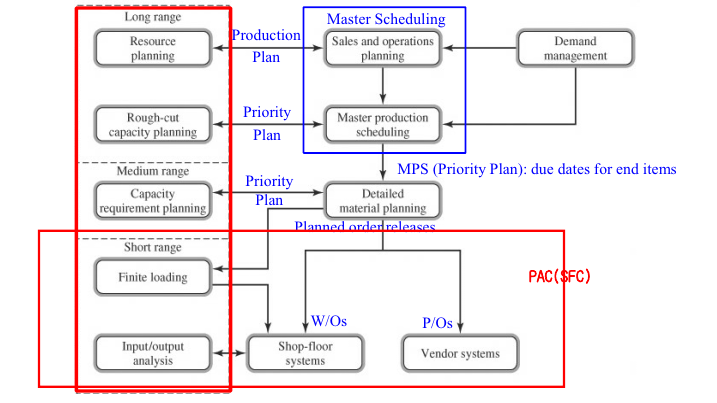
2) Links to Other MPC System modules
The primary objective of CP is to estimate capacity requriements early enough to be able to meet those requirements
CP의 주요 목표는 이러한 요구사항을 충족할 수 있을 정도로 초기에 용량 요구사항을 추정하는 것이다.
- Resource Planning ↔ SOP
- Converts SOP data to aggregate resource units
SOP 데이터를 총 자원 단위로 환산한다.
→ intermediate-term capital / labor expansion
중기 용량 / 노동 전개
- Rough-Cut Capacity Planning ↔ MPS
- Estimated capacity requirements of MPS
MPS의 예측된 자재 요구:
CPOF , Capa Bills, Resource Profiles,...
- Capacity Requirements Planning ↔ MRP
- Detailed capacity plan based on time-phased material plans
시계열 자재 계획에 기반한 자세한 용량 계획
- Input : IWP, routing, MRP data (scheduled receipts, planned orders, work calender)
- Finite Loading ↔ Material Planning and PAC (Dispatching / Sequencing)
- Adjustment of open plans due to capacity utilization
용량 활용도에 따른 개방형 계획의 조정
→ Finite Scheduling 유한 계획
- I/O Analysis ↔ PAC
- Monitoring actual consumption of capacity during execution of detailed material planning
상세 자재 계획의 실행 동안 실제 용량 소비를 모니터링
3) Major Methods
RP > CPOF > Capacity Bills > Resource Profiles > CRP
- Resource bill(SOP) → Product family
- capa bill (MPS) → producct model
(1) RP
a) Bill of Resources
- the quantity table of critical resources to make 1 unit of a product family
1 unit의 제품군을 만드는데 필요한 주요 자원의 양에 대한 데이터
b) Reconciling differences between load and capacity → 6 steps of RP process
부하와 용량의 차이 조정 → RP 프로세스의 6단계
- Determine key resources for product families
제품군의 주요 자원을 결정한다.
- Determine UOMs for key resources 주요 자원의 UOM을 결정한다
→ Aggregate unit 에 해당
- Determine available capacity for each resource
각각의 자원의 가용한 용량을 결정한다.
- Calculate load on each resource 각각의 자원에 따른 부하를 계산
- Compare load to available capacity 부하를 가용용량과 비교
- Revise production plan or adjust capacity 생산 계획을 수정하거나 용량을 조절한다.
3. Capacity Planning and Control Techniques
1) RCCP Process
- Same as the 6-step RP process with more detailed data
더 상세한 데이터를 가진 RP 프로세스 단계와 동일하다.
- Key resources → UOM → available capa → load profile(from MPS; CPOF, CB, RP) → compare and revise
- load profile = MRP 전개 이전에 진행
2) Capacity Planning Using Overall Factors (CPOF)
- Simplest approach to RCCP RCCP에서 가장 간단한 방법
- Data inputs from MPS MPS로부터 데이터 투입 ← Not planned orders
- Based on planning factors from historical data
역사적 데이터를 기반으로 한 계획 요소를 기반
: work center utilization, production standards,...
- CPOF Procedure
- Estimate overall labor/machine-hour requirements
전반적인 노동/설비 시간 요구를 추정한다
BOM에 있는 Standard 를 이용 ; W/C → Accounting Data
- Allocated to work centers based on historical workloads perecentages
역사적인 작업 부하 비율을 기반으로 작업장에 배분
- Pros and Cons
- Minimal data requirements and calculation 최소한의 데이터 요구 사항 및 계산 :
use only accounting data (cost accounting)
- Work reasonably well for JIT JIT에서 합리적으로 작동
: fast execution, low WIP
- Inherent inaccuracies may limit usefulness
내재된 비정확성은 유용성을 제한시킨다.
- Example
- Work center load = historical percentage * total required capacity
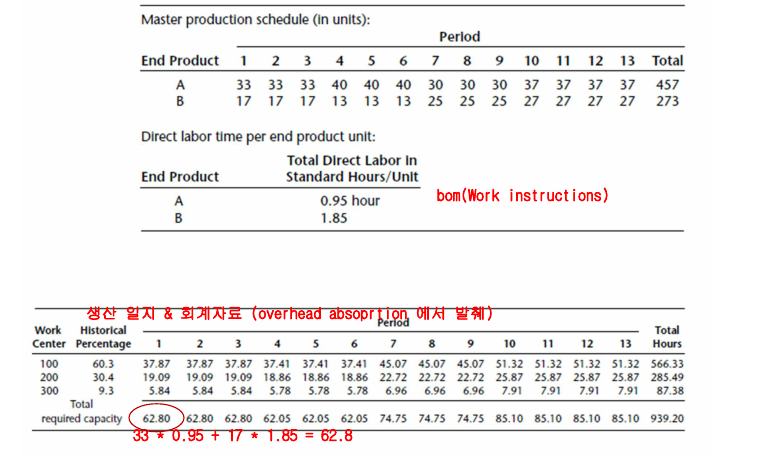
3) Capacity Bills
- More detailed RCCP method than CPOF (CPOF 보다 더 상세한 RCCP 방법)
- Provide more direct link between individual end products and work centers
각각의 말단 상품과 work center 간의 직접적인 연결을 제공한다.
- Input
- BOM, routing and standard time data (standard cost data), Bill of Capacity, MPS
- Bill of Capacity
- total standard time to produce 1 unit of an end product (by work center)
말단 상품을 1 단위 만드는데 필요한 전체 표준 시간
- MPS data
- used to estimate capacity requirements for each work center
각각의 작업장에서 필요한 용량을 추정하는데 사용된다.
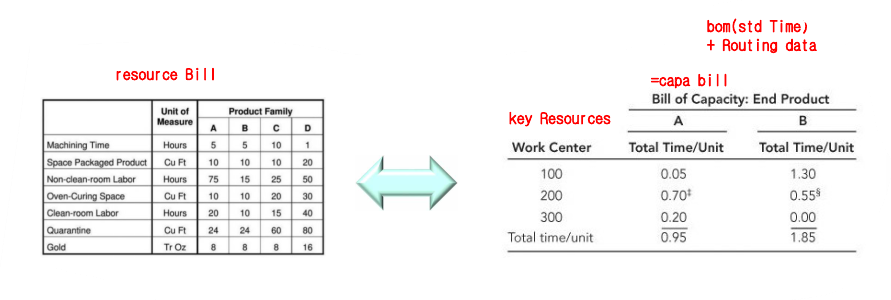
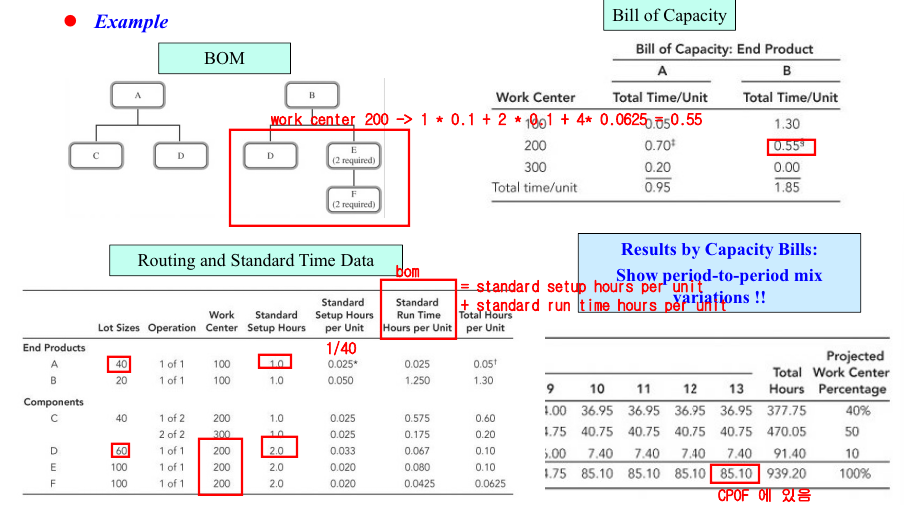
4) Resource profiles
- Most detailed RCCP technique (RCCP 기술 중 가장 상세)
- Consider production lead time information 생산 리드타임을 고려
← CPOF / CB don't consider specific timing or L/T
CPOF / CB 는 특정 타이밍이나 리드타임을 고려하지 않는다.
- Provides time-phased projections of capacity requirements for individual work centers
용량 수요를 개별적 작업장에 시계열적 적용하는 것을 제공
- More sophisticated approach but require tracking of relatively shor time period (<1 week)
좀 더 섬세한 접근 방법이나 상대적으로 짧은 시간 간격의 추적을 필요로 한다.
- Example
- Capa requirement = Requests(by work center and period) for 1 unit of end product X MPS quantity
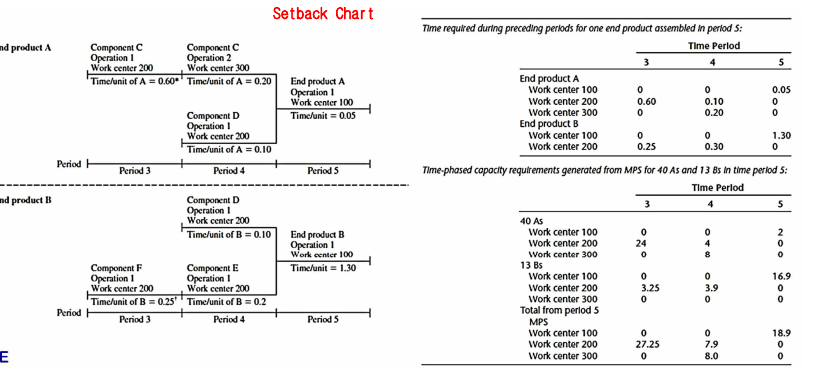
5) Detailed Capacity Planning (DCP)
(1) Overview of DCP
- DCP : the most detailed level in the capacity planning process 용량 계획 프로세스의 가장 상세한 수준이다.
- DCP Process
- Materials planned → capacity planned → resource utilization determined
- Factors in DCP
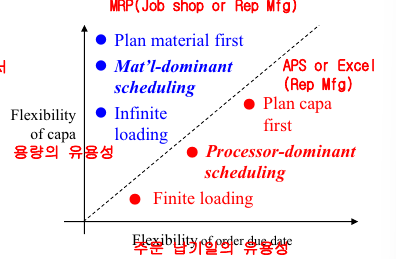
- Flexibility of capacity and scheduling 재고와 계획의 유연성
- Whether material or capa is planned first
재료와 재고가 처음에 계획되어있는지 아닌지에 따라서
- Manufacturing environment : MTS, ATO
- Types of scheduling
- Material-dominant scheduling 자재 중심 스케줄링
- MRP by due dates → Verified by CRP
납기일을 기준으로 한 MRP → CRP 에 의해 유효화
- Processor-dominant scheduling 프로세스 중심 스케줄링
- Production level by capa and inventory invenstment policies
용량에 의한 생산 수준 & 재고 투자 정책
- Production level is an input to SOP, and so to MPS & MRP
생산 수준은 SOP의 투입물이며 MPS 와 MRP에서도 마찬가지이다.
a) Work center or Cell 작업장
- ID, description, shop & shift calendar (work calendar), available time, efficiency
- Machines/operators, standard(inter-operation) L/T, scheduling reules references
- Manufacturing L/T
- queue → setup → run → wait → move → queue → setup...
- operation time = setup + run
- inter operation time = wait + move + setup
b) Load 작업 부하
- Calculation of total load 전체 부하의 계산
- Operation time/order(lot) = number of units * runtimme/unit + setup time
= planned order
- Priority data 우선순위 데이터
- Open orders, planned order releases ← MES & ERP (MRP)
- Other sources of load 작업 부하의 원인
- rework, scrap, yield, past due orders, destructive test, prototypes
- 재작업(불량품 재생) ↔ reentry (재진입 ; 정상품)
; 반도체인 경우 재진입 공정이 종종 발생한다 (정상 공정)
- Routing data
- Op. no. op. description, planned or alternate work center
← BOM or master
- UOM, standard run time per unit(piece), quantity, tooling,...
← A work center can be either machine-paced or labor paced
설비 중심 혹은 사람 중심의 작업장이 될 수 있다.
- Standard (internal/external) setup time per lot, sequence-dependent setups
순서 의존 setupt(e.g. 농도가 낮은 것부터 우선 생산)
(3) Balancing Load and capacity 용량과 부하의 균형
Review with the SOP pre-meeting team, if necessary
a) Overload condition 과부하 조건
Increase capacity and/or reduce load
- Increase capa
- Extra shifts, overtime, extra or transfer workers, cross-trained or reassign workers 다기능 작업자
- Add equipment / cellular mfg, reduce setupt time, increase process rates, subcontract or outsource
- Reduce load
- reduce lot sizes, hold orders in production control
- lot size↓ → setup cost ↑ but 재고 (the goal ; 재고를 너무 많이 만들지 말아라)
- Change the MPS, incentives to customer
b) Underload condition 부하 부족(많이 못만들고 있는 상태)
Reduce capacity and /or increase load
- Reduce capa
- adjust/eliminate shifts, temporary layoffs
- Reassign(or train) worker temporarily from direct labor job
직접 노동 작업에서 작업자를 임시로 재할당(또는 교육)
- Increase load
- make items(normally purchased or subcontracted), increase the MPS
상품을 만든다(보통 구매 혹은 위탁), MPS를 늘린다
- Release order early, increase lot sizes, subcontract work for others
c) Redistribute load 부담의 재구성
- Use alternate work centers, use alternate routing
대체 작업장, 대체 경로 사용
- Revise the MPS or lot sizes, overlap operations and split lots
MPS와 랏 크기 수정, 중복 작업 및 분할 로트
→ Lot Splitting(The goal)
- Modify priorities by adjusting operation start dates forward or backward
작업 시작 날짜를 앞뒤로 조정하여 우선 순위 수정
6) Capacity Requirements Planning
(1) Difference with CRP and RCCP
more inputs and more computing requirements
더 많은 투입물과 더 많은 컴퓨팅 기술을 요구한다
- Utilizes time-phased MRP data 시간 순서의 MRP 데이터를 사용한다.
- actual lost sizes, lead times, open/planned orders
- Takes into account materials in inventory 재고 내의 자재를 고려한다
- PAB of components and assembled products
조립된 상품과 부품의 PAB
- Accounts for the current status of WIP WIP의 현재 상태를 고려한다
← open-order data by MES
- Accounts for service parts and other demands not accounted for in the MPS
MPS에서는 서비스 파트와 다른 수요를 고려하지 않는다.
(2) Characteristics of CRP
Primarily for job shop and batch
job shop 이나 batch 에서 많이 사용
- To plan material first and to validate the material plan
자재를 먼저 계획하고 자재 계획을 유효화한다.
- To give high priorities to due dates, and to ensure delivery reliability and due-date adherence
납기 일에 높은 우선 순위를 주고 납기 신용성을 준수하며 납기일의 준수를 중요히한다.
- To regard capacity as flexible and infinite
재고가 유연하고 무한하다고 가정한다.
(3) CRP Process
- Determine load on resource 자원의 작업 부하를 결정한다. (planned order)
- Simulate scheduling of lad at W/Cs by period
각 시기별 작업장의 부하를 시뮬레이션 한다. (Sequencing)
- Methods for simulation : what-if analysis, backward scheduling → ARENA
- Create W/C load profiles (or report) 작업장별 load profile 을 만든다
- Resolve load-capacity imbalances (If not, revise MPS)
부하와 용량간의 불균형을 해소한다.(만약되지 않는다면 MPS를 수정한다)
- Revise the MPS
- evaluate the feasibility of planned orders with load profiles
load profile 을 이용하여 planned order 의 실현 가능성을 평가
- If changes in requirements(i.e. MPS or planned orders) are required,
만일 수요의 변화(MPS, planned order)가 필요하다면,
planners and management may need to take action
계획자와 관리인은 조취를 취해야 한다.
- Prepare operating plan for execution 실행을 위한 운영 계획을 준비한다.
(4) Advantages
improved accuracy in timing capacity requirements
용량 요구의 타이밍의 정확도가 높아진다
- RCCP techniques can overstate required capacity
RCCP 기술이 필요한 용량을 과장할 수 있음
- Widely applicable, Time-phased visibility of load and capacity imbalances
광범위하게 적용 가능한 로드 및 용량 불균형의 시계열적 가시성
- Confirm adequate cumulative capacity 적절한 누적 용량을 확인
- Reduce erratic L/T 불규칙한 L/T 감소
- Consider specific lot sizes and routings 특정 lot size와 경로를 고려
- Use more detailed L/T data 좀 더 상세한 리드타임 데이터를 사용
(5) Limitation
- Not applied to line or continuous production 라인형 혹은 연속형 생산에 적용되지 않는다 ; No work order(w/o)
- Solve only simple planning and scheduling problem
오로지 간단한 계획 혹은 스케줄링 문제를 해결할 뿐이다
- The effects of MPS revisions are not clear
MPS 수정의 효과가 명확하지 않다
- Require extensive and accurate input data but use approximations in scheduling load
광범위하고 정확한 input 데이터를 요구하지만 스케줄링 부하에는 추정치를 사용한다
- Not identify resource contentions and secondary constraints(e.g. tools)
자재 주장을 규명하지 않으며 부가적 제약을 고려하지 않는다
- Resource contention can occur interferences among machines
자재 제약은 설비 간 간섭을 일으킬 수 있다.
(6) Example
- Scheduled / planned quantity multiplied by processing time for work center
scheduled / planned quantity X 각 작업장 별 처리 시간
- This process is repeated for each work center to complete the plan
계획을 완수하기 위해 각각의 작업장에서 해당 프로세스를 반복한다.
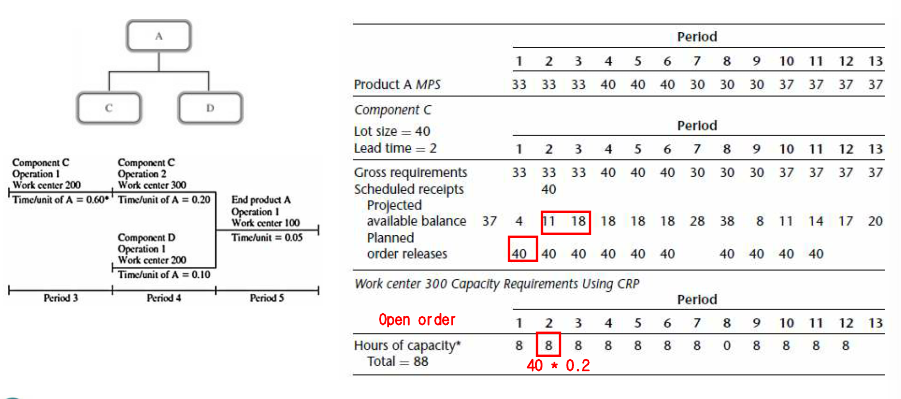
7) Comparison among CP techniques
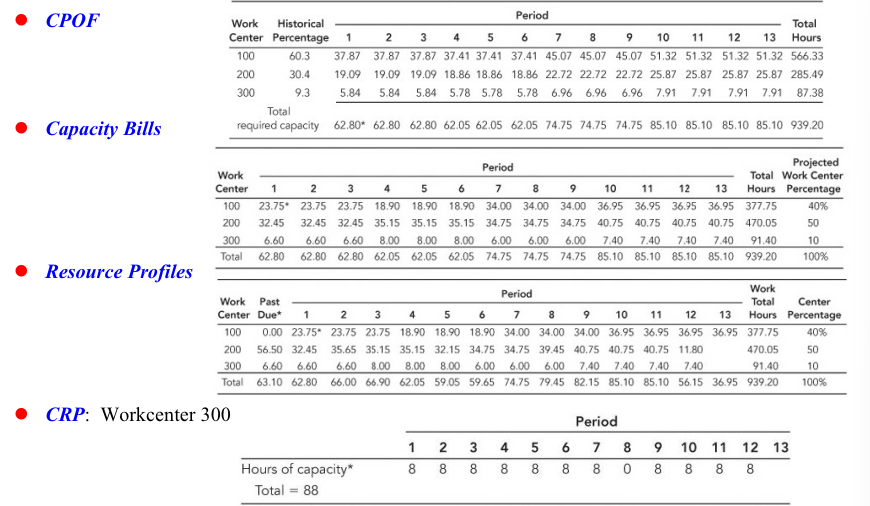
Techniques | Pros 장점 | Cons 단점 |
---|
CPOF | - easy to use 사용하기 간단하다 - Minimal computational efforts 게산 노력을 최소화할 수 있다 | - Not consider product mix, lead times, inventory, order status 제품군, 리드타임, 재고, 주문 상태를 고려하지 않는다 - Less accurate 정확도가 낮다 |
CB (Capacity Bills) | - easy to use 사용하기 간단하다 - Minimal computational efforts 계산 노력을 최소화 (CPOF < CB) - Consider product mix 제품군을 고려한다 | - Not consider lead times, inventory, order status 리드타임, 재고, 주문 상태를 고려하지 않는다. - Less accurate 정확도가 낮다 (CPOF < CB) |
RP (Resource Profile) | - easy to use 사용하기 간단하다 - Less computational efforts 계산 노력을 줄인다 (CB<RP) - Consider product mix, lead time 제품군, 리드 타임을 고려한다 | - Not consider inventory&planned order, order status 재고와 planned order, 주문 상태를 고려하지 않는다. - Less accurate 정확도가 낮다 (CB<RP) |
CRP (Detailed Capacity Planning) | - Consider product mix, lead time, inventory & planned orders, order status 제품군, 리드 타임,재고와 planned order, 주문 상태를 고려한다. - More accurate 좀 더 정확하다 | - Requires MRP/MES system & time-phased records MRP와 MES 시스템, 시계열 자료가 필요하다. -Extensive computational efforts 계산 노력이 많이 들어간다. |
4. Scheduling Capacity and Materials Simultaneously
용량과 자재를 동시에 고려하여 스케줄링
MRP does not consider capacity MRP 는 용량을 고려하지 않는다 (Infinite Scheduling)
1) Finite (Capacity) Scheduling
(1) Infinite scheduling
- CRP calculate only capacity needs CRP는 필요한 용량만 계산한다
→ Mannual adjustments for infeasibility 실행 불가능에 대한 수동 조정
(2) Finite Scheduling
- Calculating a detailed schedule for each job in each work center
각각의 작업장에 따른 업무에 대한 자세한 스케줄을 계산한다
- Establishing when a work center's capacity is not sufficient for all planned jobs
계획된 모든 작업에 대해 작업장의 용량이 충분하지 않은 경우 설정
- Prioritization / optimization rules determine which jobs will be shifted to later times
우선 순위와 최적화 규칙은 어떤 작업을 뒤로 미룰 것인지를 결정한다.
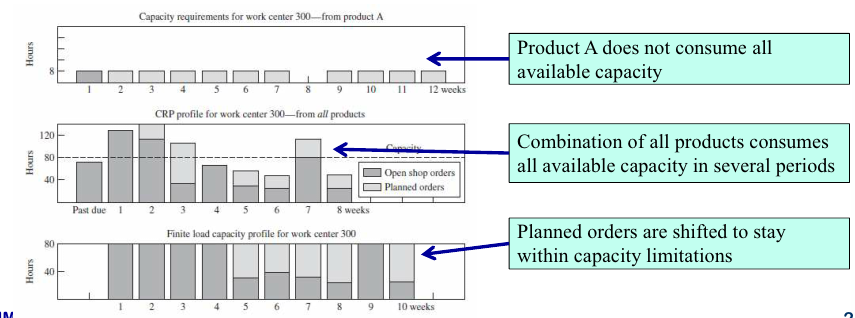
(3) Work Center Scheduling
a) Vertical loading
- scheduling independently from other work centers
다른 작업장과 독립적으로 스케줄링
→ Greedy heuristic
- Increases capacity utilization but may result in more partial job ompletion
용량 활용도를 높이지만 작업 완료가 더 부분적일 수 있음
b) Horizontal loading
- scheduling through all work centers in order of priority
우선순위에 따라 모든 작업장에 대해서 스케줄링 → optimal(?)
- Lower capacity utilization but generally a higher proportion of jobs are completed in a shorter time span (higher customer service levels)
낮은 자재 사용량을 가지나 일반적으로 높은 비율의 작업은 짧은 기간동안에 완수될 수 있다. (높은 CS 레벨)
- Front(Forward) Scheduling
- based on the earliest starts 최대한 빠른 시작을 전제(Cutting approach)
- Back(Backward) Scheduling
- based on the latest starts 최대한 느린 시작을 전제(MRP)
- Central-point scheduling (TOC 이론 ; bottle neck)
- Backward scheduling for operations before the critical operation
중요 작업 이전의 작업에 대한 backward scheduling
- Forward scheduling for the critical operation and all subsequent operations
중요 작업 및 모든 후속 작업에 대한 Forward scheduling
(4) Issues in Implementation
- Randomness leads to actual times that don't match scheduled times
무작위성으로 인해 예약된 시간과 일치하지 않는 실제 시간이 발생함
- Accuracy of the plan deteriorates over time
계획의 정확성은 시간이 지남에 따라 저하된다
- Frequent rescheduling may be needed to maintain accuracy
정확도를 유지하기 위해서는 빈번한 재계획이 필요하다
- Rescheduling
- Computationally expensive and practically infeasible
2) Finite Scheduling with Product Structures : Using APS Systems
1) Expand finite scheduling to the entire product structure
전체 제품 구조로 finite scheduling 확장
end products and sub-assenblies ; 반도체 공정 - Reentry
- Can lead to a significant reduction in leadtimes
리드타임들에 대한 상당한 감소를 일구어낼 수 있다
↔ Tons of detailed data required 많은 양의 상세 데이터가 필요
- Essentially use Horizontal loading and optimization / heuristic algorithms
기본적으로 수평 로딩 및 최적화/휴리스틱 알고리즘 사용
2) Example
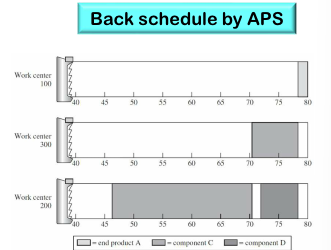
- The entire schedule for the MPS could have been fulfilled in less than 0.5 week.
MPS를 위한 전체적인 스케줄은 0.5주 보다 밑으로 충족될 수 있다.
- Executing the schedule may make some people nervous
스케줄을 이행하는 것은 몇몇의 사람들을 불안하게 만들 수 있다
- Focus on improving estimates as much as possile and thereafter focus on flawless execution
가능한 한 예측을 개선하는 데 초점을 맞춘 후 완벽한 실행에 집중
- APS will produce an overall capacity profile and detailed schedules for each work center
APS 는 각각의 작업장에 대해서 전체적인 capacity profile 과 상세 schedule을 만들 수 있다.
- The schedule may have holes (idle time) to respect the schedules for the end products
일정에는 최종 제품에 대한 일정을 준수하기 위한 구멍(공회전 시간)이 있을 수 있습니다.
- The example shows that there are many ways to skin the cat
목적을 달성하는데 있어서는 많은 방법이 있음을 보여준다
- Typically provide the ability to look at the sschedules visibly
일반적으로 일정을 시각적으로 확인할 수 있는 기능을 제공
- Allow manual intervention for what-if simulation
what-if 시뮬레이션에 수동 개입 허용
3) Features of APS
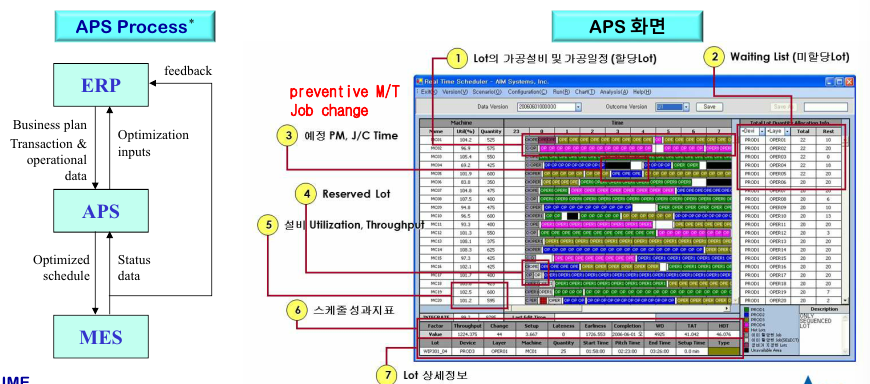
- Multiple scenarios 여러개의 시나리오
- Max, utilization, min. WIP, changes in order due dates,..
- Optimization 최적화
- Hybrid of math programming and heuristic, simulation,
- Interactive scheduling with human experts 전문가를 대동한 상호적 스케줄링
- Drag and drop, what-if simulation
- Performace management 성과 관리
- KPI estimation and evaluation
5. Management and Capacity Planning / Utilization
Capacity is one side of the coin ; Capacity management is the other
1) Capacity Monitoring with I/O Control
(1) I/O Control
The best approach to the match between planning and execution
계획과 실행을 일치시키는 가장 좋은 방법
- Planned inputs are determined by the capacity planning process
Planned input들은 용량 게획 과정에서 결정된다
- Planned outputs depend upon the nature of the work center
Planned output들은 작업장의 특성에 의해 결정된다
- Capacity constrained work center 용량 제약이 있는 작업장
- Output is determined by its processing rate
처리 비율에 따라서 산출물이 결정된다
- Non-capacity constrained work center 용량 제약이 없는 작업장
- outputs match planned inputs
산출은 planned input 과 일치한다
(2) Differences between plan and actual
- Differences between plan and actual must be addressed (management by exception)
계획과 실제의 차이는 반드시 해명되어야 한다(예외로서 관리)
- Never put into a manufacturing facility or to a vendor's facility mroe than you belive can be produced
제조 시설이나 공급업체의 시설에 { 생산될 수 있다고 믿는 이상의 제품 }을 투입해서는 안 된다
2) Managing Bottleneck Capacity
1) Theory of Constraints (TOC)
- 1 hour loss in bottle neck = 1 hour loss to the entire factory
- OPT : 1st generation APS ↔ TOC : Heuristic used for OPT
2) Basic procedure
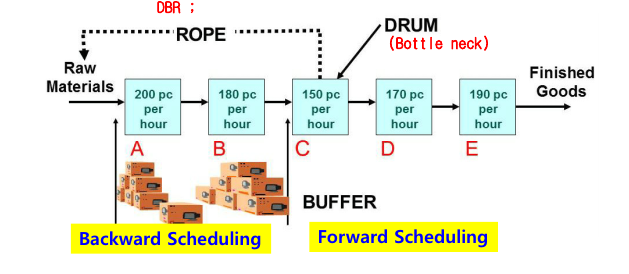
1. Determine bottle neck work centers 병목 작업장을 결정한다 use RCCP / CRP
2. Look for quick solutions to eliminate bottleneck 병목을 제거하기 위해 빠른 해답을 찾는다
▷ expand capacity or alternate routings 용량을 늘리거나 대체 경로를 찾는다
3. Concentrate scheduling efforts on managing bottleneck resources
병목 현상 자원 관리에 스케줄링 노력 집중
▷Schedule jobs that run through bottlenecks separately from non bottleneck jobs
병목에서의 작업은 비병목 작업과 별개로 스케줄을 짠다
▷ Use finite scheduling for bottleneck jobs
병목 작업을 위해 유한 스케줄링을 사용한다
- Horizontal loading and backward scheduling
3) Capacity Planning in the MPC System
Capacity is directly related to L/T & WIP ← Little's Law (L = λW)
용량은 리드타임과 WIP에 직접적으로 연관되어 있다 ; 수량 = 생산율*시간
- Short-term capacity prb can be reduced by well-executed production and resource planning
단기간 용량 문제는 잘 수행된 생산과 자원 계획에 의해 절감될 수 있다
- Efficient use of sufficient capacity by a good shop-floor system reduces capacity issues
우수한 작업장 시스템에서 충분한 용량을 효율적으로 사용하면 용량 문제가 줄어든다
4) Choosing the Measure of Capacity
- The firm's needs and constraints should determine the capacity measure
회사의 필요와 제약은 용량 측정 단위를 결정한다
- Example : labor hours, machine hours, physical lunits, monetary units
- Labor 노동
- Shrinking portion of direct labor & less labor flexibility
직접 노동의 비중 축소 및 노동 유연성 감소
- Less clear distinctions between direct and indirect labor
직접 노동과 간접 노동 간의 차이점이 명확하지 않다
5) Issues in Capacity Management
- Alternatives for changing capacity 용량 변경을 위한 대안
- Modify the MPS, customer orders, and planned capacity
- Review with SOP pre-meeting team if necessary (Middle Manager)
만약 필요하다면 SOP 프리 미팅 팀에서 검수
- Different persectives on capacity management 용량 관리에 대한 다양한 관점
: MRP, TOC, Lean
- Key performance measure 주요 성과 측정
- efficiency / utilization, performance to schedule, zero defects, inventory dollar days(IDD), stabiltiy of schedule
- 2Mat′iCost+COGS$ X LT from Purchase to Sale
6) Choice of a Specific Technique
(1) RCCP
- CPOF, Capacity Bills, Resource profiles
- Most general, widely applicable, easier to implement, useful in JIT situations
가장 보편적이며 널리 적용가능하며 쉽게 적용가능하고 JIT 상황에서 유용하다
- Less powerful
(2) CRP
- Effective with MRP
- Require more data and computational effort 더 많은 데이터와 계산 노력이 필요하다
- Only applicable in conjunctiton with MRP MRP와 함께만 적용 가능
→ Unnecessary (or Impossible) under JIT (No W/O)
(3) APS
- Most sophisticated alternative 가장 섬세한 방법론 ; MPS Planned order level에서도 사용
- Highest levels of effort 가장 많은 노력을 기울여야 한다
- High levels of accuracy possible with good data and flawless execution
좋은 데이터와 결점 없는 실행 하에서는 가장 정확하다
(4) DCP in Manufacturing Environments
Continuous | Repetitive | Batch | Job shop | Project |
---|
Process flow scheduling APS Localized use of other methods | Simplified, Lean(kanban), APS | MRP &CRP, APS Lot-sizing is important | MRP&CRP, APS | CPM,PERT,Critical chain,APS |
7) Using the Capacity Plan
- Two broad choices are available when actual capacity and plan are mismatched
실제 용량과 계획이 일치하지 않을 때 두 가지 범용적인 선택이 가능하다
- Change capacity 용량을 바꾼다
- reduce or increase capacity as indicated(within constraints)
표시된 대로 용량을 줄이거나 늘린다(제한된 범위 내에서).
- Overtime/undertime, alternate routing, material subsitution
- Make or buy, subcontracting
- Revise material plan 자재 계획 수정
- change requirements and / or timing to match available capacity
가용한 용량에 일치하도록 필요량 혹은 타이밍을 수정한다
- The amount of material that can be produced is limited by the available capacity, regardless of the material plan
자재 계획과 상관 없이 생산할 수 있는 자재의 량은 가용 용량에 의해 제한된다
(1) Interactions with master scheduling and production control
마스터 스케줄링과 생산 제어 간 상호작용
a) Master scheduler = Material Manager
- Monitors key work centers 주요 작업장 감독
→ revise data in the RCCP DB as necessary 필요에 따라 RCCP의 데이터베이스의 데이터를 수정한다.
b) Production controller
- Weekly plan sharing, order release, prioritization rule for dispatching
주간 계획 공유, 주문 릴리스, 발송 우선순위 지정 규칙
- Order status update, past-due orders identified and rescheduled
주문 상태 업데이트, 기한 초과 주문 확인 및 예약 변경
- Bottleneck evaluated
8) Capacity Management in Repetitive Manufacturing
(1) Issues in Repetitive Manufacturing
Line scheduling ↔ Line balancing
- RP for new plant capacity 새로운 공장 용량을 위한 RP
→ Line balancing replaces RCCP and CRP 라인밸런싱은 RCCP와 CRP를 대체한다
- Ass'y line or operation should produce at the market demand rate, takt time
Assy 라인 또는 운영은 시장 수요율, 소요 시간대로 생산해야 한다.
(2) Line Balancing
a) A plan-materials-first and due-date-driven approach
- In lean capacity management, line balancing creates value through product quality and sales
Lean 용량 관리에서 라인 밸런싱은 제품 품질과 판매를 통해 가치를 창출합니다.
- Line balancing is but one of many tools to reduce WIP and L/T
라인 밸런싱은 WIP와 리드타임을 줄이기 위한 많은 도구 중 하나이다.
b) Line balancing process
- Identify individual tasks or activities to be performed
수행되어야 하는 개별 업무 혹은 활동들을 확인한다.
- Determine the takt time required to perform each task
각각 업무를 수행하는데 필요한 소요 시간을 확인한다.
- Establish precedence constraints, if any, for each task
만약 존재한다면 선행 제약을 확인한다 → Precedence Diagram (N/W)
- Determine the required assembly line output and the total time available to produce
필요한 어셈블리 라인 출력 및 생산에 사용할 수 있는 총 시간 결정
- Calculate the required cycle time (time btw product completions)
필요한 사이클 타임(제품 완수 사이의 시간)을 계산
- Determine the theoretical min # of workers and assign task to workers
이론적으로 최소 작업자의 수를 확인하고 작업자에게 업무를 할당한다
- Assess the effectiveness of the solution 해결책의 효과성을 평가
9) Capacity Management in Service Industries
(1) Capacity Issues in Service Industries
- Job variability, demand 변동이 심함, Not inventoriable
- Hard to determine and measure service capa
서비스 용량을 결정하고 측정하는데 어려움이 있다
- RP/RCCP/CRP can be used, but need to represent the variability in service operations
RP/RCCP/CRP는 사용 가능하지만 서비스 운영에 있어 다양성을 표현할 필요가 있다
- The role of queue in service L/T should be considered
서비스 리드타임에서 queue의 역할을 고려해야 한다
(2) Service Capacity Management Strategies
Increase or decrease service capacity
서비스 용량을 늘리거나 줄이는 것
- Workforce level, cross training employees, part-time workers
노동력 수준, 다기능 작업자, 비정규직
- Service hours, better scheduling tools and practices
- Equipment, automation tech, facilities
- Customer participation (e.g. Kiosk)
10) Capacity Management in Process Industries
(1) Process Industries
- Manufacturing by mixing, separating, forming and/or performing chemical reaction
- Chemicals, paper, food and dairy, sugar, textiles, rubber, steel,...
- key characteristics
- divergent product structure 서로 다른 제품 구조
- value added in planning capa, continuous flow
- production process structure 생산 프로세스 구조
- Similar to BOM in discrete industries 이산 산업에서의 BOM과 비슷
- Hierarchy
- Division >> plant >> process train >> stage >> process unit
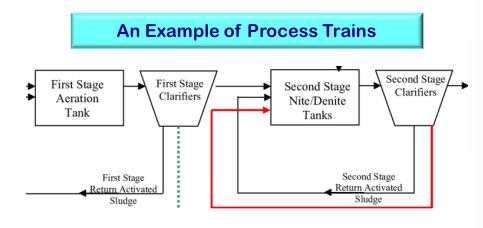
(2) Process Flow Scheduling
- Scheduling calculations are guided by the process structure
스케줄링 계산은 프로세스 구조에 의해서 안내된다
- Stages are scheduled using processor-dominated or material-dominated scheduling processes
스테이지는 프로세서 중심 혹은 자재 중심 스케줄링 프로세스들을 사용하여 계획되었다
- Process trains are scheduled by reverse-flow, forward-flow, or mixed flow scheduling
프로세스 트레인은 reverse-flow, forward flow, mixed-flow 스케줄링에 의해 계획되었다
- Reverse-flow↔backward scheduling ; forward-flow ↔ forward scheduling
6. Summary
1) Principles
- Capacity plans must be developed concurrently with material plans if the material plans are to be realized
자재 계획이 실현되려면 자재 계획과 동시에 용량 계획을 개발해야 합니다.
- Capacity planning techniques must match the level of detail and actual company circumstances
용량 계획 기법은 세부 수준 및 실제 회사 상황과 일치해야 합니다.
- Capacity planning can be simplified in JIT environments
용량 계획은 JIT 환경에서 단순화될 수 있다
- Better resource and production planning processes lead to less diffficult capacity planning processes
더 나는 자재 및 생산 계획 프로세스는 좀 더 쉬운 용량 계획 프로세스를 야기한다
- Better shop-floor systems reduce the need for short-term capacity planning
더 나은 shop-floor 시스템은 단기간 용량 게획의 필요성을 줄인다
2) CPIM Questions
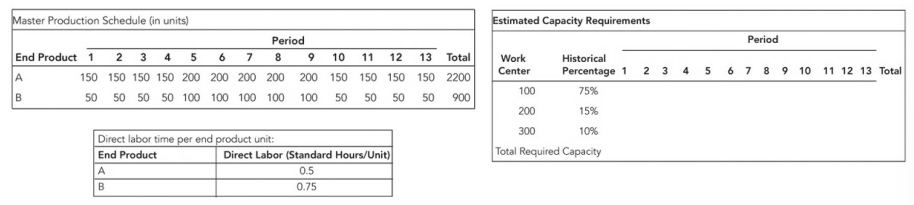
What is the total required capacity (in standard hours) for period 2? (choose the best answew)
a. 100
b. 110
c. 120
d. 130
answer : b (150 0.5 + 50 0.75)
What is the required capacity in work center 100 for period 6? (choose the best answew)
a. 100
b. 110
c. 120
d. 130
answer : d (200 0.5 + 100 0.75) * 0.75 = 131.25
What is the total required capacity in work center 200 over 13-period planning horizon? (choose the best answew)
a. 200
b. 250
c. 300
d. 350
answer : b (2200 0.5 + 900 0.75) *0.15 = 266.25
When capacity does not match the plan, wich of the following actions can be taken?
I. Provide sufficient capacity
II. Change the material plan
III. Modify capacity calculation
a. I only
b. II only
c. I and IIonly
d. I and III only
answer : c
Resource profile planning differs from capacity planning using overall facotrs(CPOF) and capacity bills by considering which following?
a. Customer order
b. projected workload in individual work centers
c. Future capacity expansions
d. Inventory plans
answer : b
In which of the following ways does capacity requirements planning (CRP) differ from roug-cut capacity planning techniques?
I. CRP uses a time-phased approaches
II. CRP considers service part demand
III. CRP considers standard lot sizes
a. I only
b. II only
c. I and II only
d. I,II, III
answer : c
According to the theory of constraint(TOC), which of theses conditions is most desirable?
I. 100% utilization of bottleneck work centers
II. 100% utilization of non-bottleneck work centers
III. less than 100 % utilization off bottleneck work centers
a. I only
b. II only
c. I and II only
d. I,II, III
answer : a
Which of the following are capacities that may need to be managed?
I. Direct labor
II. Inspection
III. Engineering
a. I only
b. II only
c. I and II only
d. I,II, III
answer : d