0) Detailed Material Planning
A basic tool for performing the DMP function in the manufacture of component parts and their assembly into finished items
구성 부품 및 부품 조립을 완제품으로 제조할 때 DMP 기능을 수행하기 위한 기본 도구
(1) Material Planning in different Environment ─ 서로 다른 환경에서 자재 계획
a) Project and ETO
- Unique products, low volume, large scale, long duration → PM(Project Mgmt)
특별한 상품, 작은 수량, 대규모, 장기간 → 프로젝트 관리
- Project Management
- Work packages → WBS (Work Breakdown Structure) - based PMS (PM system)
- WBS (Work = jobs to do) ↔ CBS(Cost = project COA) ↔ OBS(Organization unit in charge)
- Release of order releases offset lead times against due dates
주문 릴리스의 릴리스는 납기일에 대한 리드 타임을 상쇄합니다.
b) Process Flow
- High volume, MTS, capital intensive, line(similar) routings with continuous flow
대규모, MPS, 높은 자본 집양적, 연속 공정의 라인 라우팅 (비슷한 경로)
- Production schedules authorize work
생산일정에 따라 작업이 승인된다
→ There are no W/Os 워크 오더가 존재하지 않는다
- Processor-dominated scheduling : finite scheduling for capacity first
프로세서 중심의 스케줄링: 먼저 용량에 대한 유한 스케줄링
- Materials are planned and scheduled to fit with the finite schedules
자재는 유한한 계획에 알맞도록 계획된다
- Material-Dominant scheduling : production triggered by inventory level
자재 중심의 스케줄링 : 재고 수준에 의해 유도되는 생산
- Production quantity is set to target or fixed
생산량은 목표 혹은 고정으로 적용된다.
c) Lean
- Stable and continuous demand, low-variety not complex product, tackt time driven
안정적이고 지속적인 수요, 복잡하지 않은 낮은 다양성, 시간 기반
- Kanban pull system moves materials → There are no W/Os
칸반(풀 시스템)이 자재를 이동시킨다. → 워크 오더가 존재하지 않는다
- Supplieres are constantly updated on supply requirements → Long term agreement
공급자가 지속적으로 공급 필요를 조정한다 → 장기간 동의
d) Job-Shop and ATO → MRP environment
- Either push or pull, intermittent/irregular demand
푸시와 풀, 그리고 정기적 / 비정기적 수요를 모두 포함한다.
- Complex requirements for time-phased component due dates by irregular demand for end items
최종 품목의 불규칙한 수요로 인한 시간 단계 구성 요소 만기일에 대한 복잡한 요구 사항
(2) Background of MRP System MRP 시스템의 배경
- Evolution of Scientific Mgmt (F. Taylor)
테일러에 의한 과학적 관리 기법의 발전
- No formal process for SFC before Taylor 테일러 이전에 공적인 SFC 프로세스가 존재하지 않았다.
→ Planned order release and sequencing
- No lot-sizing rule 랏 사이징 룰이 없었다
→ BOM-based gross-to-net explosion for minimizing WIP
WIP 최소화를 위한 BOM 기반 총망 폭발적 증가
- Application of leading-edge computers
최첨단 컴퓨터의 적용
→ COPICS/MAPICS by IBM
(3) Objectives of MRP MRP의 목적
- To provide the right parts at the right time to meet the schedules for completed products
완제품을 위한 계획을 충족시키기 위해 올바른 제품을 적합한 시간에 제공하는 것
- The bridge between master planning(or MPS) and production in the factory
공장에서의 생산과 주 계획(MPS)간의 연결고리
- Determine requirements and keep priorities current
요구 사항 결정 및 최신 우선 순위 유지
- React to changes in supply and demand
수요와 공급의 변화에 따라 재반응
- Expedite, de-expedite, add,cancel, or change W/O and P/O
W/O 및 P/O의 신속한 처리, 추가, 취소 또는 변경
1) MRP in MPC
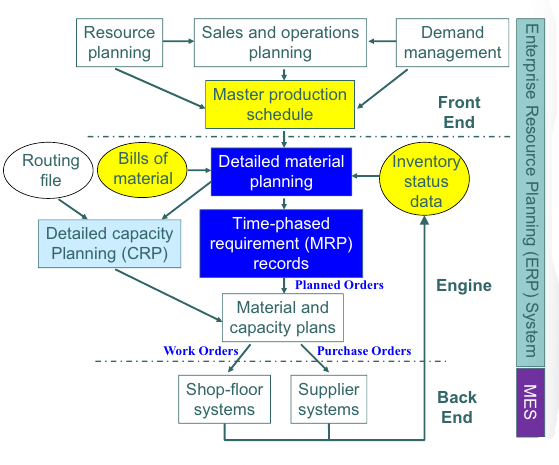
- MPS: Verified by RCCP RCCP에 의해 규명된
- BOM with routing data 경로 데이터를 포함한 BOM
- Planning factors 계획 요소 : Lot size, L/T, SS, scrap and yield,...
- Inventory status data 재고 상태 데이터
- Allocations 배치 ↔ Unallocated qt'y 배치되지 않은 양
- Scheduled receipts 계획된 수주
(2) Iteractive Procedure
(3) Major Outputs
- Schedule of planned order 계획된 주문의 계획
- Action massages 행동 메세지
2) Record Processing
(1) The MRP Time-Phased Record or MRP Grid
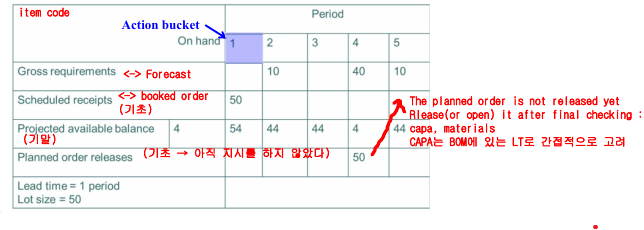
▷ The planned order is not released ye Release(or open) it after final checking : capa, materials
용량은 bom 에 있는 리드 타임으로 간접적으로 고려
- Time-phased 시계열
- stated on a unique period-by-period basis 독특한 시간별로 명시되어 있다.
← Neither aggregated nor average 총합도, 평균도 아니다
- Time bucket = period(week or day)
- Planning horizon = # of periods in the plan
- Gross requirements
- anticipated usage of demand for the single item(part no.) during each period
각 시기에 따라 하나의 아이템에 대한 수요에 사용될 것으로 예상되는 사용량
- Scheduled receipts
- existing replenishment(or open) orders at the beginning of period
기초에 남아있는 재고 보충 오더
- Projected available balance 기말재고
- The current and projected inventory status at the end of period
시기의 마지막, 현재 혹은 예측되는 재고 상태
- Planned order release
- Planned replenishment orders for the begining of each period
기초에 주문할 오더
(2) An example of BOM
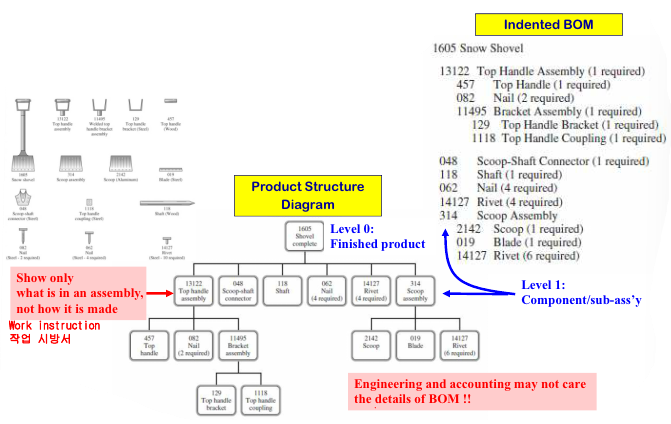
- Shows the components and sub-assemblies to physically produce a product
제품을 물리적으로 생산하기 위한 구성 요소 및 하위 어셈블리를 표시합니다.
- Show only what is in an assembly not how it is made
어떤 것을 조립해야 하는가만 보여주지 어떻게 만드는지는 알려주지 않는다;
Work Instruction 작업시방서
- Enginnering and accounting may not care the details of BOM
공학과 회계는 BOM의 상세 내역을 신경쓰지 않는다.
(3) BOM Processor for RDB 관계형 DB에서의 BOM 프로세서
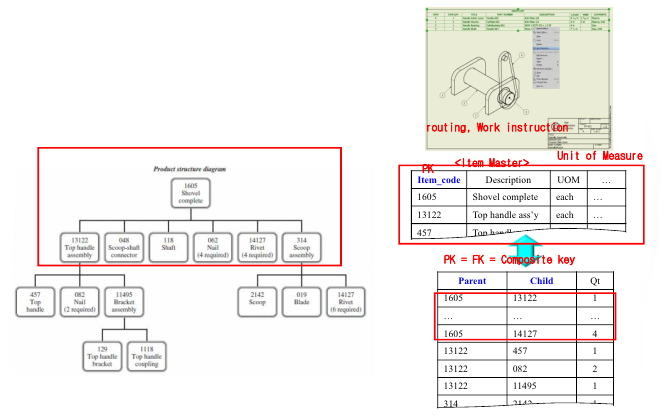
- Engineering drawing : item_code + BOM
- Item Master: item_code + attribute1+...
- Single-level BOM : parent-child relationships
- BOM processor : display / manage BOMs
(4) Gross to Net Explosion
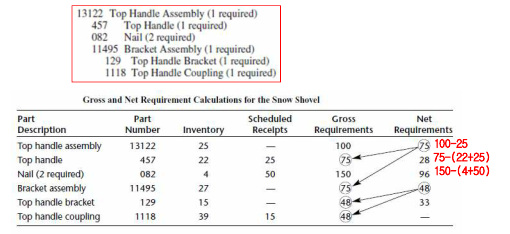
Explosion 전개
The process of translating product requirements into component part requirements
상품 요구량을 구성 요수 요구량으로 번역하는 작업
- Need to take existing inventories and scheduled recipts into account
현재 가지고 있는 재고와 예상되는 공급을 회계에 반영해야 한다.
- Only the components net of any inventory is considered
모든 재고의 구성 요소 순만 고려된다
→ Linked throught the system
- Gross requirements = total planned usage 전체 계획된 사용량
- Net requirements = gross requirements - (inventory + scheduled receipts)
전체 요구량 = 총 수요 - (재고량 + 예측된 수주량)
(5) Summary of MRP Explosion Process MRP 전개 과정의 요약
a) Explosion Process
- Find the low-level code of each item
각각의 품목의 하위 레벨의 코드를 찾는다.
- Calculate net requirements using netting process at level 0
0 수준에서 Netting Process(b) 과정을 이용하여 전체 수요량을 계산한다.
- Create scheduled receipts, PAB, and planned order releases for level 0 items
end item에 대한 계획된 주문, PAB, 그리고 계획된 주문 발주를 만든다.
- Post to corresponding gross requirements period for level 1 items, exploded for quantity per.
레벨 1 품목에 대한 해당 총 요구 기간으로 게시하고, 당 수량으로 분해합니다.
- Repeat netting and creation of planned orders through the lowest level
최하위 수준까지의 netting 과 creation 과정을 반복한다.
b) Netting (Gross-to-Net) Process
- Calculate OHB (On-Hand Balance)
- Balace equation : Previous PAB + scheduled receipts - gross requirements / allocations
- Preliminary PAB = OHB - ss (safety stock)
- Final PAB =
- if pre-PAB ≥ 0 ; Pre-PAB
- if pre-PAB < 0 ; pre-PAB + planned order receipt
(6) Generating Planned Orders of Workcenters and Suppliers
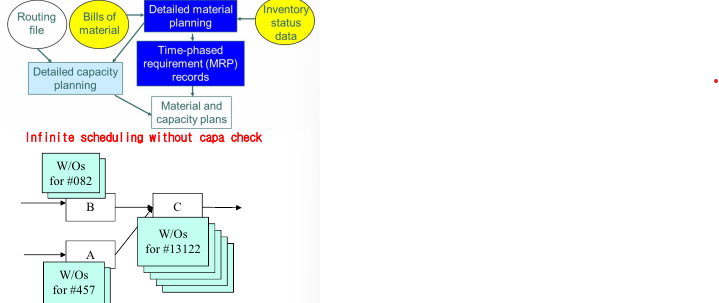
a) MRP Explosion MRP 전개
- MPS of an end item → MRP records of part no's
- MRP records do not specify workcenters/suppliers
MRP에서는 작업반이나 공급업체를 특정짓지 않는다.
b) Planned orders generated by routing data 라우팅 데이터에 의해 만들어지는 예측 주문
- MRP records of part no's → Planeed orders
- Infinite scheduling without capa check
(7) Lead Time Offsetting
-
Determine when each component is needed
각각 어떤 구성 요소들이 언제 필요한지를 결정하는 것
; Gross-to-net explosion tells us how many but when
- Two factors : lead times and precedent relationships
- Work-Center L/T :
move(upstream) → queue → setup → run → wait → move → queue (downstream)
; Setup → Run = Operation Time
-
MRP uses the benefits of back scheduling and the gross-to-net explosion → Heart of MRP
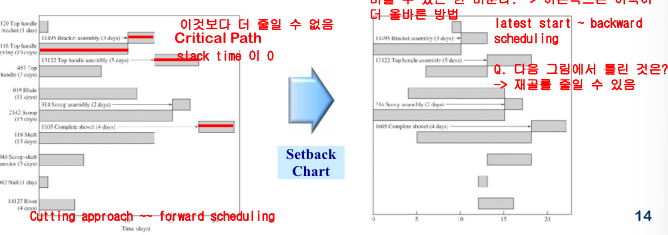
- Front Schedule
- Will start everything as soon as possible (earliset start)
모든 것은 최대한 빠르게 시작한다.
- Cutting (Forward scheduling)
Every components required start at the same time 동시에 시작하기를 요구된다
Cutting (or traditional)approach does not follow the MRP principle
Cutting (전통적) 방식은 MRP 방식을 따르지 않는다.
- Back schedule
- will start everything as late as possible (latest start)
가능한한 느리게 모든 것을 시작한다. (최대한 느리게 시작)
미룰 수 있는 것은 최대한 미룬다.
- Reduced inventories, Minimize the storage time, Postpone
Backward Scheduling | Forward Scheduling |
---|
User MRP logic : works back from MRP due date to determine operation start time 작업 시작 시간을 결정하기 위해 MRP 만료 날짜로부터 다시 작업 | Material producrement and operation scheduling start as an order is received 주문 접수 시 자재 생산 및 작업 일정 시작 |
Last operation scheduled first 마지막 작업이 먼저 예약됨 : preceeding op's scheduled back from start of the successive op 연속 작업 시작부터 작업의 예약된 되돌리기 | Operations usually scheduled from the first op to the last op 일반적으로 첫 번째 작업부터 마지막 작업까지 예약된 작업 |
Less inventory buildup than forward scheduling forward scheduling 보다 재고 증가율 감소 | More inventory build up than backward scheduling Backward scheduling 보다 재고 증가율 증가 |
When must this be started to finish by due date? 마감일까지 와수하려면 언제부터 시작되어야 하는가? | If I start now, when can I have it? 내가 지금 시작하면 언제 받을 수 있는 것인가? |
Used when low inventory is a top priority and production is synchronized with due date? 재고 부족이 최우선 사항이고 생산이 마감일과 동기화되는 시기에 사용. | Used When resources are underloaded or capacity costs are high, and load leveling is desired 리소스가 부족하거나 용량 비용이 높고 로드 레벨링이 필요한 경우 사용 |
(8) Linking the MRP Records
a) Lot Sizing Rule
- Lot for Lot(LFL / L4L)
make only what is needed → Exactly matches net requirements
필요한 것만 만들기 → 순 요구사항과 정확히 일치
- Fixed quantity
usually based on EOQ → Quantity in multiples of lot size → Class C items
일반적으로 EOQ 기준 → 로트 크기의 배수로 된 수량 → Class C 항목
b) Pegging ← Implosion process
- show the source of requirements
요구의 원천을 보여준다.
- Single level vs. full pegging
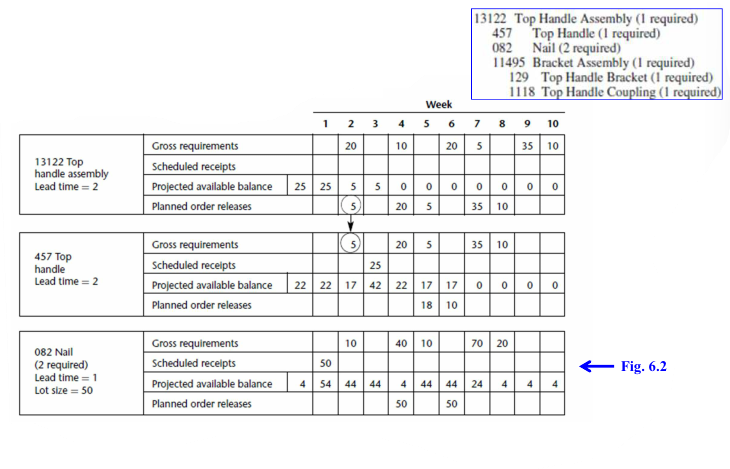
3) Technical Issues
Major parameters : planning frequency and horizon, time buckets
얼마나 자주 MRP를 짤 것인가 / 시간 단위는 얼마나 할 것인가
(1) Events affecting the priority plan 우선순위 계획에 영향을 미치는 사건
- External events
- Customer 고객 : changes to customer orders 고객 주문의 변화
- Suppliers 공급자 : shortages, late deliveries 불량, 늦은 배송
- Internal events
- Process : lower yields 떨어진 수율, higher scrap factors 높은 폐기율
- Late / early completions, capacity shortages 늦은 / 이른 완성, 용량 부족
- Inaccurate inventory record 부정확한 재고 실사
⇒ Actions Available to the Planner 계획자가 할 수 있는 행위들
- Maintain priorities 우선순위 유지
- Expedite, de-expedite, change qt'y
- Replanning 재계획 : Changes in end-item due dates 최종 품목 납기의 변화
(2) Processing Frequency : System Nervousness vs. Out-of-Date W/Os
- Regeneration : processing all records in one computer run
한 컴퓨터에서 모든 레코드 처리 ⇒ 그 전에 있던 MRP 가 없었다고 가정하고 새로 다시 Planning
- All part numbers are completely reconstructed each time the records are processed
레코드가 처리될 때마다 모든 부품 번호가 완전히 재구성됩니다.
- More frequent runs create more credibility but may lead to system nervouseness
더 자주 실행할수록 신뢰성이 높아지지만 시스템불안도가 높아질 수 있다.
- Net change : alternative to regeneration
Regeneration 의 대안책 ⇒ 어떤 포인트를 기점으로 그 부분만 고침 (APS)
- Respond to the need for frequency by processing only the records affected by the change.
바뀌는 부분만 처리함으로서 빈번한 변화에 대한 대응을 한다.
- Can reduce computer time enough to make daily run ( or even real time processing)
매일의 변경을 충족할 수 있을 정도로 (혹은 실제 시간 처리까지도) 컴퓨터 처리 시간을 줄일 수 있다.
- Do a generation to clean up all the records every once in a while
한 세대씩 모든 레코드를 정리합니다.
- Discrete Optimization(IP) 의 특성
- 숫자에 예민하다.
- System robust 가 약하다 ⇒ Net Change 를 잘 하지 않는다.
(3) Bucketless System
- Use the exact release and due dates for each requirement → Smaller buckets mean more buckets
각 요구 사항에 대한 정확한 릴리스 및 만료 날짜 사용 → 버킷이 작을수록 버킷 수가 늘어남 (주→일→시간 단위)
(4) Lot Sizing
a) LFL
- too simple-minded to consider economic trade-offs or physical factors
경제적인 트레이드 오프나 물리적인 요소를 고려하기에 너무 간단한 방법이다.
- Usually used for intermediate sub-assembly
보통 중간 부품들에게 사용되는 방식이다.
b) Lot sizing
- Usually used for the end-item and basic component levels → Discrete lot sizes
보통 최종 제품 혹은 기본 구성 단계에서 많이 사용된다. → 이산 랏 사이즈들
- Cascading effect 파급(폭포) 효과
- Batching at one level significantly increase requirements at the lower levels
한 레벨에서 일괄 처리하면 하위 레벨에서 요구 사항이 크게 증가
(5) Safety Stock and Safety Lead Time
- MRP = Infinite loading 상정 ; BOM을 통해 간접적으로 SS 유지
a) Safety Stock
- buffer stock over and obove the quantity needed to stisfy gross requirements
총 요구량을 만족시키는 양보다 더 많도록 완충 역할을 하는 제고
- Used when quantity uncertainty is the issue → When?
수량 불확실성이 문제가 될 때 사용
b) Safety Lead Time
- order are released and scheduled to arrive earlier than they should
반드시 받아야 하는 날보다 좀 더 일찍 발주 혹은 계획을 하는 주문
- Used when timing of orders is the issue 주문의 시기가 중요할 경우 사용
(6) Low level coding
- In order to process all common parts at the same time
모든 공통 부품을 한번에 처리하기 위해
- All gross requirements have been passed down to a part before its MRP record is processed
MRP 레코드가 처리되기 전에 모든 총 요구 사항이 부품으로 전달되었습니다.
(7) Pegging vs. Where used Data
a) Pegging record
- Part numbers (or planned orders) associated with a current gross requirement
현재 총 요구량에 관련된 파트 넘버(혹은 계획 주문)
- Link between planned / customer orders and the gross requirements → Reverse of explosion
계획된/고객 주문과 총 요구사항 간의 연결 → 전개의 역방향
- Can track the impact of problem (e.g. material shortage) back to orders it will affect
문제(예: 자재 부족)가 영향을 미칠 주문에 미치는 영향을 추적.
b) Where-used data
- Indicate for each part number, the part numbers of all items where it is used.
각 부품 번호에 대해 해당 부품이 사용되는 모든 품목의 부품 번호를 표시. (bom 상에서 어디에 쓰이는가)
- Show all the parents whether or not there is a current requirement for the part.
부품에 대한 현재 요구 사항이 있는지 여부를 모든 상위 level에게 보여 준다.
- Assess aggregate impact of costing change and component scarcity.
원가 변화와 구성 요소 부족이 미치는 전체적 영향을 평가
(8) Firm planned orders (FPO)
- planned order which can't be changed by a MRP run or regeneration
MRP나 Regeneration으로는 바꿀 수 없는 계획 주문
- Regeneration will lead to large numbers of planned order changes
Regeneration 은 계획 주문 변화에 많은 영향을 미칠 것이다.
- Temporaily overriding the MRP logic to provide stability
안정성을 보장하기 위해 MRP의 논리를 일시적으로 덮어씌운다.
- Extra processing might be required 추가적인 처리가 필요하다.
(9) Service Parts
- Any significant service part demand must be included in the MRP record
어떠한 중요한 서비스 부품 수요도 MRP 레코드에 포함되어야 한다.
- 완제품 → MPS → MRP ; A/S → MPS / MRP
(10) Planning Horizon
a) Longer planning horizon
- increases computational requirements 계산적인 요굴를 더욱 늘린다.
b) Shorter planning horizon
- may result in less-effective plans 덜 효과적인 계획이 될 수 있다
- Should cover the cummulative lead time for all finished goods items
모든 최종 제품에 대해서 누적적 리드 타임을 고려해야 한다.
- Example : MPS covers 3 months only, if the cummulative L/T is 9months?
(11) Scheduled Receipts vs. Planned Order Releases
(a) Planned orders
- only a plan → can be changed more easily
계획 뿐 → 좀 더 쉽게 바뀔 수 있다.
- When a planned order is released, it impacts gross requirements
만일 planned order 가 발주된다면 총 요구량에 영향을 미친다.
- Effects of releasing planned orders planned order을 발주할 시 효과
- become an open order or job ticket
open order 혹은 job ticket 이 된다.
- Appear as a scheduled receipt in MRP
MRP에서 scheduled receipt 로서 보여진다.
- Allocate components to the order → picking slip
주문에 구성 요소가 할당된다. → picking slip
(b) Scheduled receipt
- Actual commitment (P/O, W/O) : more difficult to change
실제 수락 (P/O, W/O) : 좀 더 바뀌기가 어렵다.
- Scheduled receipts for open shop orders already have component materials assigned
오픈 숍 주문에 대한 scheduled receipt에서 구성 요소가 할당됨.
(b) Scheduled receipts
4) Using the MRP System
Issues in successful MRP 성공적인 MRP의 고려할 점
MRP planner, exception codes, bottom-up replanning, MRP system output
1) MRP planner
Typically in the production planning, inventory control and purchasing departments
일반적으로 생산 계획, 재고 관리 및 구매 부서를 의미한다.
- Release orders 주문 발주
- purchase orders, shop floor (work) orders → P/O & W/O
- Reschedule orders 주문 재계획
- change due dates of existing open orders (when desirable)
기존 미결 주문의 마감 날짜 변경(필요한 경우)
- Analyze and update parameter 파라미터의 분석 및 수정
- lot sizes, L/Ts, scrap allowances, safety stocks,...
- Reconcile errors or inconsistencies 오류 또는 불일치 조정
- eliminate their root causes 근본 원인을 제거한다.
- Find key problem 주요 문제를 찾는다.
- take action to preevent future crises 미래 위험을 막는 행위를 취한다.
- Use the system to solve shortages 부족을 해결하기 위해 시스템을 이용
- adjust records and system parameters to prevent recurrence
재발 방지를 위해 레코드 및 시스템 매개 변수 조정
- Enhance the system 시스템 개선
- improve performance for the planner's job easier
기획자의 업무를 보다 쉽게 수행하다.
a) Order launching
- Releasing orders from the action bucket
action bucket 으로부터 주문을 발주
- converting planned orders to scheduled receipts
planned order 을 scheduled receipts 로 바꾼다.
- May consider shrinkage allowance and other process yield situations
수축 허용량 및 기타 공정 수율 상황을 고려할 수 있다.
b) Allocation and availabiltiy checking 할당 및 가용성 확인
Availability checking 가용성 확인 → allocation (picking tickets / slips) → physical stock retrieval 물리적 재고 회복
- prior to order launching, an availability check should be done fore the necessary components
주문 시작 이전에 가용성 확인은 필수적인 구성에 대해서 완수되어야 한다.
- picking tickets to the stockroom after allocation and availability checking
할당 및 가용성 확인 후 창고로 가는 picking ticket
2) Exception codes (or Exception Reports)
- Separating the vitial few (10~20%) from the trival many : check data accuracy first
중요한 소수를 많은 다수에게서 분리 : 데이터 정확도를 먼저 확인하여라.
- Part numbers with planned order in the immediate period (or the action bucket)
즉시 기간(또는 작업 버킷)에 계획된 순서가 있는 부품 번호
- Orders with unsatisfactory timing or quantity : update MRP records
만족되지 않은 시기 혹은 수량을 가지는 주문 : MRP 레코드를 갱신
- MRP systems assume a past-due scheduled receipt will be received in the next period
MRP 시스템은 지나버린 기한의 Scheduled reciept 는 다음 period에서 받을 것이라고 가정한다.
- Unsatisfied requriements of level-0 quantity : management input needed
레벨 0 수량의 불만족 요구사항 : 경영의 투입 필요
- Possible actions 가능한 행위들
- expedite order, delay an order / scheduled receipt, cancel a scheduled receipt
신속한 주문, order / scheduled receipt 지연, order / scheduled receipt 취소
3) Bottom-up Replanning
- Using pegging data to guide efforts to solve material shortages
자재 부족을 해결하기 위한 노력을 안내하기 위해 pegging data 를 이용한다.
- pegging data shows if actual customer orders are impacted
pegging data 는 실제 고객 주문에 영향을 미치는지 아닌지를 보여준다.
4) MRP system output
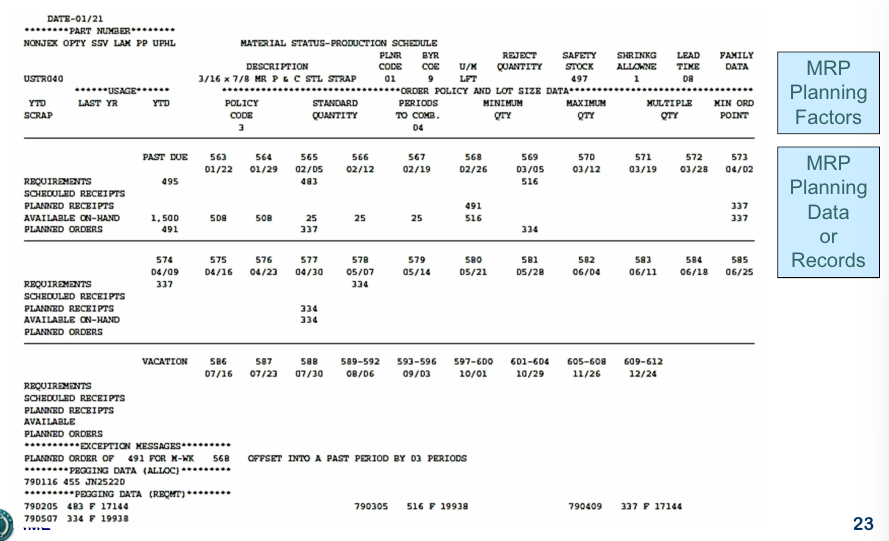
5) System Dynamics
How to correctly run the MRP system 어떻게 MRP 시스템이 올바르게 운영되는가
(1) Transactions during a period
- production status checking 생산 상태 확인 → releasing orders & picking tickets
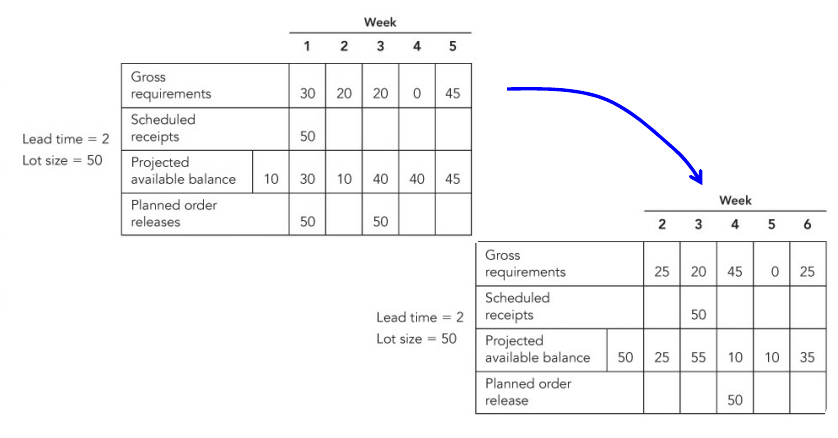
- procedural indadequancies
- An error of as little as 1 peice can cause severe problems
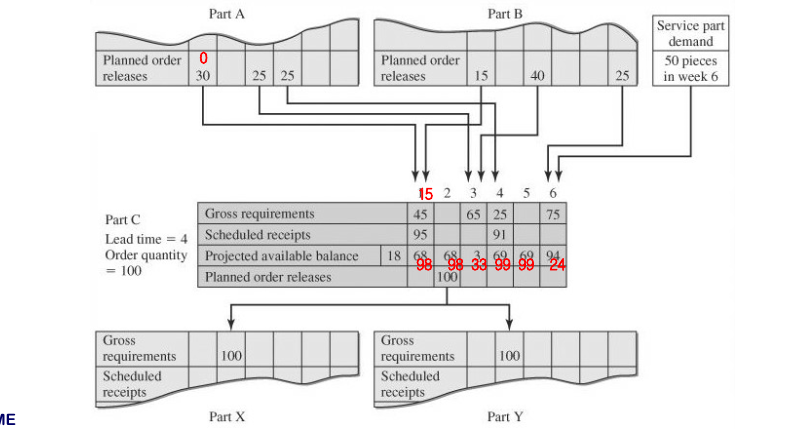
(2) Maintaining the Material Plan
a) Factors That affect the material plan
- Changes to MPS
- new order, customer orders(due dates and quantities), machine breakdowns,...
- Changes to BOM
- Changes to inventory
- receipt of parts / end items, inventory balance corrections
b) Changes to the Material Plan
① Offline MRP Simulation
- run what-if analysis, test different planning parameters,...
② Planning parameters
- L/T, lost size, SS, safety L/T, scrap factor, kanban, cycle time,...
- Planned order quantity = planned order receipt / (1-scrap factor)
- Cycle time = actual time between the completion of twoo discrete units of production
- CT≥tackt time : buffer inventory are used until improvement are able to shorten CT → 양이 부족하다.
- orders (W/O, P/O) released on time, # of changes to orders, due date of orders met
- Action message trends, downtime due to (material) shortages, excess inventory
6) Summary
(1) Concluding Principles
- Effective use of an MRP system allows development of a forward looking approach to managing mateerial flows.
MRP 시스템을 효과적으로 사용하면 물질 흐름을 관리하기 위한 전향적 접근 방식을 개발할 수 있다.
- The MRP system provides a coordinated set of linked product relationships, which permits decentralized decision making for indivudual part numbers.
MRP 시스템은 개별 부품 번호에 대한 분산된 의사 결정을 허용하는 조정된 연결 제품 관계 집합을 제공한다.
- All decisions made to solve problems must be implemented within the system, and transactions must be processed to reflect the resultant changes.
문제를 해결하기 위해 내린 모든 결정은 시스템 내에서 실행되어야 하며, 그에 따른 변화를 반영하기 위해 트랜잭션이 처리되어야 한다.
- Effective use of exception messages allows attention to be focused onthe vital few rather tan the trivial many
예외 메세지를 효과적으로 사용하는 것은 중요한 소수를 사소한 다수보다 더 주의 깊게 볼 수 있도록 한다.
(2) Summary of Project Management
PM covers the project / ETO environment
a) Project
- an endeavor with a specific objective to be met the due date and resource limitations
기한과 자원의 한계를 충족시키기 위한 구체적인 목표를 가진 노력
b) Phases of a project
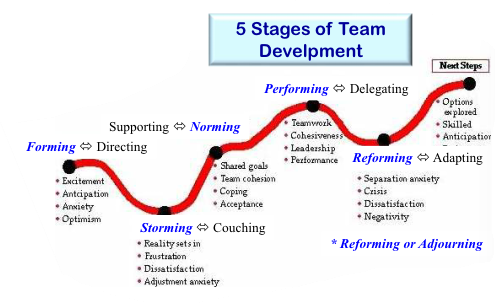
1. Initation
- why and what determines the objective, duedate and resources → Assign the PM
목적과 납기일 그리고 자원을 결정짓는 것과 그 이유
- Planning
- SOW(Statement of Work ; 작업명세서),WBS, project schedule, responsibility assignment matrix (OBS), budget,...
- Scheduling methods
- Gannt charts, CPM, PERT, critical chain method... → APS
- Project budgeting
- CBS, labor costs, material costs, equipment costs, vendor / consultant costs
- Execution
- forming the project team 프로젝트 팀 결성
- scheduling work 작업 스케줄링
- managing team realations, schedule, and budget
팀 관계, 스케줄, 그리고 예산 관리
- Monitoring and controlling
- Variance from plan ↔ Corrective action
- Closure
1) Document the project 프로젝트의 문서화
2) Conduct post-implementation audit 구현 후 감사 수행
3) Prepare and submit the final report 최종 레포트 준비 및 제출
4) Closure meeting and close operations
7. CPIM Problems
Material requirements planning (MRP) systems perform which of these functions?
1. Translating the overall production plan into detailed steps
2. Providing information for capacity planning
3. Providing information for staffing plans
a. 1 only
b. 1,2 only
c. 1,3 only
d. 1,2 and 3
answer : b
Assuming there are 5 top handle assemblies (ITEM 13122) already in inventory, how many nails would be required to produce 15 complete shovels (Item 1605) (Item 082 in the BOM, p 188)
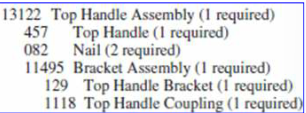
a. 20
b. 40
c. 60
d. 70
answer : a
Which of the following items is a sub assembly (produced from component) parts?
I. 13122
II. 11495
III 2142
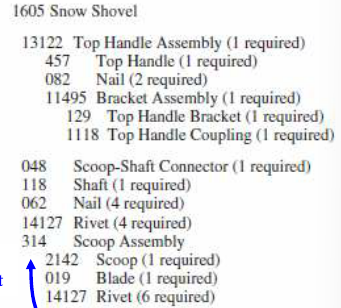
a. I only
b. I and II only
c. II and III only
answer : b
In system where timing of production is uncertain, it would more appropriate to utilize
a. Safety Stock
b. Safety Lead Time
c. Either would perform adequately
d. Neither would be appropriate
answer : b
A commitment to an external supplier (e.g. a purchase order) is represented in the material requirements planning system by a
a. Scheduled receipt
b. Planned order
c. Either a scheduled receipt or a planned order
d. Neither a scheduled receipt nor a planned order
answer : a
Which of the following is not an action commonly taken an mrp planner
I. Release order
II. Confirm inventory counts on incoming shipments
III. Reconcile MRP errors
a. I only
b. II only
c. III only
d. All are MRP planner actions
answer : b